Get Reliable Expansion Joints for Your Plant - Fast Shipping Available!
By:Admin
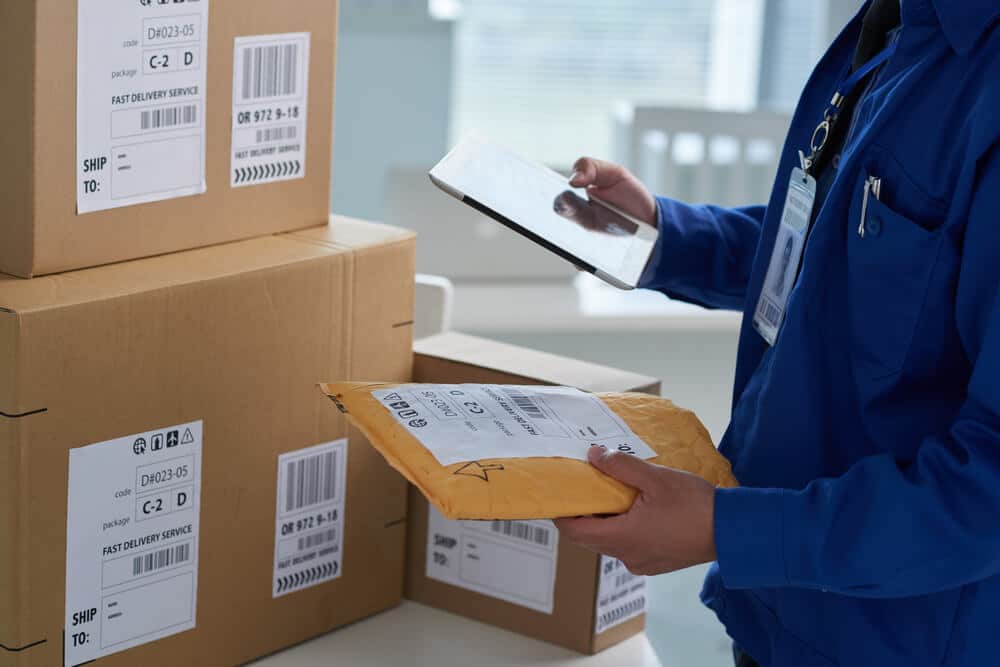
Expansion joints are an important component in many industrial processes. They are used to absorb vibrations, compensate for thermal expansion, and reduce noise. A flanged rubber expansion joint is a type of expansion joint that is commonly used in piping systems to absorb these kinds of mechanical and thermal stresses.
What is a Flanged Rubber Expansion Joint?
A flanged rubber expansion joint is a flexible element that is designed to absorb movement in piping systems caused by thermal expansion, machinery vibration, or seismic activity. The joint uses a series of convolutions or corrugations that allow it to expand and contract without damaging the piping. These convolutions are made from flexible rubber, which is why the joint is referred to as a rubber expansion joint.
The flanged ends of the joint are bolted to the piping system to provide a leak-proof seal. These flanges can be made from a variety of materials, including carbon steel, stainless steel, or plastic. The type of flange used will depend on the application and the compatibility with the piping system.
Why Use a Flanged Rubber Expansion Joint?
There are several reasons why a flanged rubber expansion joint may be necessary in a piping system. One of the primary reasons is to compensate for thermal expansion. When a piping system is exposed to temperature changes, the metal expands and contracts. If the system does not have enough flexibility to accommodate this movement, it can cause damage to the system or nearby equipment. A flanged rubber expansion joint absorbs the movement caused by thermal expansion, reducing the stress on the piping system.
Another reason to use a flanged rubber expansion joint is to absorb vibration from machinery or seismic activity. In a piping system that is connected to a piece of machinery, vibrations can be transmitted to the system, causing damage over time. A flanged rubber expansion joint reduces the amount of vibration that is transmitted to the system, protecting the piping and any nearby equipment.
Flanged rubber expansion joints also reduce noise in piping systems. When a piping system is under stress, it can create a significant amount of noise. A flanged rubber expansion joint absorbs the stress, reducing the noise levels in the system.
Choosing the Right Flanged Rubber Expansion Joint
Choosing the right flanged rubber expansion joint for your application requires careful consideration of several factors. These include the size of the joint, the type of flange, and the material of the joint.
The size of the joint will depend on the diameter of the piping system and the amount of movement that needs to be accommodated. Flanged rubber expansion joints are available in a range of sizes to fit various piping systems.
The type of flange used will depend on the compatibility with the piping system and any nearby equipment. Carbon steel and stainless steel flanges are commonly used, but plastic flanges may be necessary in certain applications.
The material of the joint will depend on the temperature and chemical compatibility of the piping system. Rubber is a common material used in flanged rubber expansion joints, but other materials, such as neoprene, can be used in applications with high temperatures or exposure to certain chemicals.
Conclusion
Flanged rubber expansion joints are an essential component in many piping systems. They provide flexibility to accommodate movement caused by thermal expansion, machinery vibration, or seismic activity. Choosing the right flanged rubber expansion joint requires careful consideration of several factors, including size, flange type, and material. With the right joint, you can reduce stress on your piping system, protect nearby equipment, and reduce noise levels in your facility.
Company News & Blog
Machining Services for Efficient Manufacturing - Suppliers and Exporters
Title: Unveiling the Essence of Machining Services: The Backbone of Industrial ManufacturingIntroduction:In the world of industrial manufacturing, precision and efficiency form the pillars of success. The implementation of cutting-edge machining services has revolutionized the manufacturing landscape, enabling businesses to meet market demands with utmost precision and versatility. In this blog, we will explore the significance of machining services in the industry, shedding light on some key aspects and benefits. Join us on this informative journey as we dive into the world of machining services.Chapter 1: Understanding Machining Services1.1 Defining Machining Services:Machining services are a comprehensive range of processes that involve the removal of material from a workpiece to achieve the desired shape, size, and functionality. These services encompass a broad spectrum of techniques like milling, turning, drilling, grinding, and more. By utilizing advanced machinery and tools, machining services cater to various manufacturing sectors, such as automotive, aerospace, electronics, and medical industries.1.2 The Significance of Machining Services:Machining services play a pivotal role in industrial manufacturing due to the following reasons:- Precision: Machining services deliver unparalleled precision, ensuring the accurate creation of complex parts and components with high conformance to specifications.- Efficiency: With the advancement of automation and computer numerical control (CNC) technologies, machining services have become incredibly efficient, reducing human errors and increasing productivity.- Versatility: Machining services can handle a wide array of materials, ranging from metals to plastics and composites, enabling manufacturers to diversify their product offerings.Chapter 2: The Key Processes of Machining Services2.1 Milling:Milling involves the removal of material from a workpiece using rotary cutters. It is widely used to create various shapes and features, such as flat surfaces, slots, pockets, and contours.Keywords: milling services, precision milling, CNC milling2.2 Turning:Turning is the process of removing material from the workpiece using a single-point cutting tool while the workpiece rotates. It is utilized to create cylindrical shapes, such as shafts, rods, and tubes.Keywords: turning services, CNC turning, precision turning2.3 Drilling:Drilling is the process of creating holes in a workpiece using specialized drill bits. It enables the integration of fasteners, connections, and facilitates fluid passages.Keywords: drilling services, precision drilling, CNC drilling2.4 Grinding:Grinding involves the abrasive removal of material to achieve a refined surface finish or to precisely shape components. It is commonly used for creating complex geometries and achieving tight tolerances.Keywords: grinding services, precision grinding, surface grindingChapter 3: The Benefits of Machining Services3.1 Enhanced Product Quality:Machining services ensure the production of high-quality components with minimal surface imperfections, ensuring the overall quality and performance of the end product.3.2 Increased Efficiency:The integration of automation and CNC technologies in machining services enables faster and more accurate production, reducing lead times, and increasing operational efficiency.3.3 Cost-effectiveness:By utilizing machining services, manufacturers can optimize material usage, minimize waste, and reduce manual labor costs, contributing to overall cost-effectiveness.3.4 Customization and Flexibility:Machining services offer immense flexibility, allowing manufacturers to cater to specific requirements and swiftly adapt to changing market demands.Conclusion:In conclusion, machining services form the bedrock of industrial manufacturing, enabling businesses to achieve precision, quality, and efficiency in their operations. From milling and turning to drilling and grinding, these services play a crucial role in shaping a wide range of components and products across diverse industries. Embracing modern machining techniques adds value to businesses and empowers them to stay competitive in a rapidly evolving marketplace. So, leverage the power of machining services and unlock a world of endless possibilities in manufacturing.
CNC Machining Parts Manufacturers in China – High-Quality and Reliable Suppliers for Precision Machining Parts
s, Manufacturers, Factory, Suppliers, Precision CNC Machining PartsChina CNC Machining Parts - The Backbone of the Manufacturing SectorCNC (Computer Numerical Control) machining has revolutionized the manufacturing sector over the last few decades, and today, it is an integral part of the industry. As the name implies, CNC machining involves the use of computers to control the movements of machines, making the process precise, accurate, and fast. CNC machining finds applications in almost all manufacturing sectors, from aerospace to pharmaceuticals, defense to automotive, and electronics to construction.China, one of the largest manufacturing hubs in the world, has emerged as a leader in the CNC machining industry. Chinese CNC machining parts manufacturers have been supplying precision parts to various industries worldwide, making China a go-to destination for businesses looking for high-quality and low-cost CNC machining parts.Why China for CNC Machining Parts?The Chinese manufacturing industry has evolved by leaps and bounds over the last few decades, thanks to the country's low labor costs, lenient regulations, and government support. China's CNC machining sector has also grown significantly, with several manufacturers popping up across the country, catering to domestic and international markets.China, being one of the most populous countries globally, has a vast workforce, making it easier for CNC machining parts manufacturers to find skilled labor. Moreover, the availability of raw materials like steel, copper, aluminum, and others is plentiful, keeping the production costs low. The Chinese government's support for the manufacturing sector and its relentless push for technological advancements has made China a hub for innovation, making the Chinese CNC machining parts more reliable and efficient.BEST PRECISION CNC Machining Parts Manufacturers - The Leading CNC Machining Parts SupplierBEST PRECISION CNC Machining Parts Manufacturers is a renowned CNC machining parts manufacturer based in China. They are engaged in the production of high-quality, low-cost CNC precision parts for various industries.Their state-of-the-art manufacturing facility is equipped with the latest CNC machines, and they employ skilled technicians to produce high-precision CNC machining parts that meet their clients' demands. They use computer-aided design and manufacturing (CAD/CAM) software to ensure their parts' precision and accuracy. BEST PRECISION CNC Machining Parts Manufacturers is committed to providing their clients with the highest quality and most reliable CNC machining parts.Their manufacturing capabilities include CNC milling, turning, drilling, tapping, grinding, and more. They produce CNC machined parts from various materials, including steel, aluminum, brass, bronze, copper, titanium, and plastics.ConclusionChina has become a popular destination for businesses looking to acquire high-quality, low-cost CNC machining parts. The country's rapid economic growth and government support for the manufacturing sector have transformed China into a hub for innovation and precision manufacturing. BEST PRECISION CNC Machining Parts Manufacturers is one such Chinese manufacturer that has made a name for itself in the industry, producing high-quality CNC machined parts for various industries. With their state-of-the-art facility and skilled workforce, they are poised to become a leading CNC machining parts supplier in the coming years.
Discover the Definition and Function of Angled Blades for Air or Water Thrust
Title: The Mighty Device Propelling the World: Motor Rotor ShaftIntroduction (100 words):Propellers, also known as propellors, are essential devices that play a crucial role in propelling aircraft or boats through air and water. Composed of a spinning shaft and angled blades, propellers create a thrust force that propels vehicles forward. In this blog post, we will explore the significance of propellers and delve into the intricate details of their key component - the motor rotor shaft. Join us as we unravel the wonders of this remarkable invention and understand its importance in the world of aviation and marine transportation.Body:I. The Foundation of Propellers (200 words):A. Understanding Propellers and Their Purpose: Propellers are dynamic mechanical devices designed to convert rotational energy into thrust force by utilizing specially designed blades. They are employed in a wide array of applications, including aviation and marine transportation.B. Key Components and Their Functions: - Blade Structure: The angled blades of a propeller are responsible for thrust generation. They are carefully engineered to achieve optimal performance. - Hub Assembly: The hub connects the blades to the motor rotor shaft and ensures stability during operation. - Motor Rotor Shaft: The motor rotor shaft forms the core of the propeller system, transmitting rotational energy from the engine to the blades.II. The Powerhouse Behind Propellers: The Motor Rotor Shaft (400 words):A. Definition and Purpose: The motor rotor shaft is a critical component of the propeller system. It acts as a bridge connecting the engine or motor to the blades, facilitating the transfer of rotational energy required for propulsion.B. Construction and Materials: Motor rotor shafts are commonly made from high-strength metals such as stainless steel or titanium to withstand heavy loads and rotational forces. They undergo precise manufacturing processes and are often subjected to rigorous quality checks to ensure durability and efficiency.C. Design Considerations: - Length and Diameter: Motor rotor shaft dimensions are determined by various factors, including the size and type of the propeller, as well as the power requirements of the engine. - Weight Optimization: Careful weight distribution is crucial to maintain the balance and efficiency of the propeller system, thereby reducing vibrations and increasing overall performance. - Strength and Flexibility: The motor rotor shaft should be sturdy enough to withstand stress and torque forces while maintaining flexibility to prevent catastrophic failure.D. Propeller Compatibility: Motor rotor shafts are designed to cater to specific types of propellers, taking into account factors like blade count, mounting mechanism, and rotational speed requirements. Compatibility ensures optimal performance and longevity of the propeller system.III. The Significance of Motor Rotor Shaft in Aviation and Marine Transportation (300 words):A. Aviation Sector: 1. Aircraft Propellers: The motor rotor shaft, along with other propeller components, enables aircraft to achieve lift and propulsion by generating thrust. 2. Performance Enhancement: Advanced motor rotor shaft designs contribute to improved fuel efficiency, reduced noise levels, and increased maneuverability.B. Marine Transportation: 1. Boat Propellers: Motor rotor shafts play a crucial role in powering watercraft, including leisure boats, commercial vessels, and even submarines. 2. Increased Efficiency: Innovations in motor rotor shaft technology allow for higher propulsion efficiency, resulting in reduced fuel consumption and lower carbon emissions.Conclusion (100 words):Propellers stand as a testament to human progress in conquering the skies and seas. At the core of these dynamic devices lies the motor rotor shaft, effectively transmitting rotational energy to enable propulsion. With ongoing advancements and continuous research, motor rotor shafts are becoming more versatile, robust, and efficient than ever before. From aircraft soaring across the skies to boats navigating vast oceans, propellers equipped with motor rotor shafts remain indispensable. By understanding the complexities and significance of motor rotor shafts, we gain an even deeper appreciation for the remarkable engineering that drives transportation in the modern world.
Decorative Square Pipe Flange for Sewer and Industrial Scenes - Available in Antique Silver, Iron and Rust Finishes
Custom Aluminum CNC Machining Parts - China Manufacturer and Supplier
Title: China's Leading Machining Supplier: Revolutionizing the Industry with Custom Aluminum CNC Machining PartsIntroduction:In today's fast-paced manufacturing world, precision and quality play a crucial role in satisfying the ever-growing demands of a diverse range of industries. Custom machining services, particularly CNC milling, turning, multi-axis milling and turning, and automatic lathing, have become indispensable in achieving unparalleled accuracy and efficiency. In China, Dongguan Fuxulai Metal & Electronic Co., Ltd. has established itself as a prominent market leader specializing in OEM and ODM custom aluminum CNC machining parts. Let's delve deeper into their expertise and understand how this company is transforming the machining landscape.Precision CNC Machining:Dongguan Fuxulai boasts state-of-the-art CNC milling machines that possess incredible accuracy and advanced functions. With these cutting-edge devices, the company ensures that they meet the most stringent requirements of their clients. By employing computer-controlled tools, this machining supplier can craft complex aluminum parts with absolute precision, which eliminates human error and ensures consistent quality time after time.Moreover, their proficiency in CNC turning allows them to manipulate the rotational aspect of the material, offering a broad range of contours, grooves, and shapes. By combining milling and turning processes, the engineers at Dongguan Fuxulai can produce intricate designs with superior dimensional accuracy, enabling their clients to achieve impressive results.Multi-Axis Milling and Turning:To cater to even more intricate and demanding projects, Dongguan Fuxulai offers multi-axis milling and turning services. These advanced techniques involve the utilization of computer-controlled equipment capable of working on multiple axes simultaneously. This innovation allows for the creation of complex geometries and contours, giving their clients a competitive edge in their respective industries.Automatic Lathing:With automatic lathing, Dongguan Fuxulai showcases their commitment to efficiency and productivity. By utilizing high-tech automatic lathes, they ensure fast and precise cutting and shaping of aluminum materials. This highly automated process significantly reduces production time while guaranteeing impeccable quality. Such efficiency is invaluable for businesses striving to meet demanding timelines without compromising on quality.Reliability and Collaborative Approach:Dongguan Fuxulai's reputation as a reliable China lathing machining supplier extends beyond their exceptional machining capabilities. They understand the importance of clear, effective communication throughout the entire manufacturing process. Their experienced team diligently collaborates with clients, paying attention to every detail of their requirements. This approach ensures that the final product aligns perfectly with the client's specifications and expectations.Meeting Global Standards:In an increasingly competitive market, adhering to international standards is crucial. Dongguan Fuxulai is committed to excellence and complies with strict quality regulations to provide products that meet or exceed global standards. Their commitment to maintaining stringent quality control measures during the entire production process ensures consistent superior performance of their custom aluminum CNC machining parts.Conclusion:Dongguan Fuxulai Metal & Electronic Co., Ltd., a leading China lathing machining supplier, is revolutionizing the machining industry with their expertise in CNC milling, CNC turning, multi-axis milling and turning, and automatic lathing. With a dedication to precision, efficiency, and collaboration, they provide customized solutions that adhere to the highest quality standards. By choosing Dongguan Fuxulai, clients can enjoy the benefits of cutting-edge technology, impeccable craftsmanship, and unrivaled customer satisfaction, solidifying China's position as the go-to destination for top-notch machining services.
Get High Precision Custom CNC Parts Delivered to Bath Easily
Title: High Precision Custom CNC Parts Empowering Industries in BathIntroduction:In a world where precision, efficiency, and speed are crucial for businesses, the advent of CNC (Computer Numerical Control) machining has revolutionized the manufacturing sector. Bath, renowned for its innovative industries, is now at the forefront of benefiting from high precision custom CNC parts produced by a network of professional CNC machine shops. These parts are not only competitively priced but also facilitate quick lead times, making the sourcing of custom components easier than ever before.CNC Machining Parts - Enabling Excellence:With a rich history in manufacturing and engineering, Bath has always been open to embracing technological advancements that enhance productivity. CNC Machining Parts, a leading CNC machining service provider in the region, specializes in producing highly accurate custom parts that meet the diverse requirements of various industries.The company's sophisticated CNC machines, guided by computer-aided design (CAD) software, ensure precise production to exact specifications. From intricate components for the automotive and aerospace sectors to cutting-edge medical devices, CNC Machining Parts consistently delivers exceptional quality, reliability, and durability.Competitive Pricing and Cost Savings:One of the key advantages of sourcing custom CNC parts through CNC Machining Parts is the competitive pricing that benefits businesses in Bath. The company's extensive network of professional CNC machine shops enables them to offer cost-effective solutions without compromising on product quality or accuracy.By streamlining the manufacturing process and eliminating the need for manual labor, CNC machining significantly reduces overhead costs. Bath-based industries can, therefore, leverage this advantage to enhance their competitiveness in the market, secure lucrative contracts, and drive growth.Quick Lead Times and Efficient Production:Time is of the essence in the fast-paced business world. CNC Machining Parts excels in delivering custom CNC parts with unbeatable lead times, owing to their well-established network of machine shops. By systematically coordinating the production process, the company expedites manufacturing while maintaining the highest level of precision.Whether businesses require a single prototype or a large production run, CNC Machining Parts ensures efficient and timely delivery, fueling Bath's industries with an uninterrupted supply chain. This capability enables companies to meet project deadlines promptly, reducing downtime and accelerating their time-to-market.Versatile Application in Various Industries:The applications of custom CNC parts are diverse, catering to a wide range of industries in Bath. CNC Machining Parts serves as a reliable partner for businesses operating in sectors such as automotive, aerospace, robotics, medical devices, electronics, and more.The company's expertise in precision machining allows for the creation of complex geometries, ensuring optimal performance and functionality for each industry-specific requirement. Whether it is a critical engine component in an automotive assembly line or a delicate surgical instrument for a medical procedure, Bath-based industries can rely on CNC Machining Parts to deliver reliable solutions tailored to their needs.Local Collaboration and Partnership Opportunities:CNC Machining Parts, being based in Bath, not only fulfills the local demand for custom CNC parts efficiently but also fosters collaborative partnerships with businesses in the area. By engaging with the local industry, the company understands the unique challenges faced by Bath-based manufacturers and provides them with tailored solutions.Through strategic collaborations, knowledge sharing, and innovation-driven initiatives, CNC Machining Parts further contributes to the growth and development of Bath's industrial landscape. The resulting synergies have the potential to reinforce Bath's reputation as a hub of technological advancement and excellence in manufacturing.Conclusion:The availability of high precision custom CNC parts in Bath, courtesy of CNC Machining Parts, has transformed the manufacturing sector in the region. With competitive pricing, quick lead times, and a commitment to delivering excellence, the company empowers businesses to stay ahead of the curve. By harnessing advanced machining technologies, Bath-based industries now have access to reliable custom components that drive innovation, efficiency, and success across a wide range of applications.
Enhancing Ecommerce Experience for Higher Checkout Conversion Rates
Transforming the Ecommerce Experience to Improve Checkout Conversion RatesIn today's digital age, ecommerce has become an integral part of our lives. With the convenience of online shopping, consumers have come to expect seamless and engaging experiences when it comes to making a purchase. As an online retailer, it is crucial to understand that ecommerce experiences directly impact checkout conversion rates. In this blog post, we will explore how you can transform your ecommerce experience to increase sales.While there are several factors that contribute to checkout conversion rates, one of the key aspects is the overall user experience. A clunky and confusing website can be a major turn-off for potential customers, leading them to abandon their carts before completing the purchase. Therefore, it is important to optimize your website's design and navigation to provide a seamless and intuitive experience.To customize your ecommerce website, you can utilize various technologies and tools available in the market. One such tool is Customized Bolt, which provides a range of features to enhance the shopping experience. With Customized Bolt, you can personalize the checkout process according to your specific business needs. By incorporating this tool into your ecommerce platform, you can create a tailored experience that resonates with your target audience.Here are a few ways in which you can use Customized Bolt to transform your ecommerce experience and improve checkout conversion rates:1. Simplify the Checkout Process: With Customized Bolt, you can streamline the entire checkout process, making it quick and easy for customers to complete their purchase. By eliminating unnecessary steps and reducing the number of required fields, you can significantly reduce cart abandonment rates.2. Implement a Responsive Design: In today's mobile-driven world, it is essential to have a website that is optimized for various devices and screen sizes. Customized Bolt allows you to create a responsive design that ensures a seamless browsing experience for your customers, regardless of the device they use.3. Enhance Product Descriptions and Images: An appealing product presentation plays a crucial role in influencing purchase decisions. With Customized Bolt, you can showcase your products in a visually appealing manner, with high-quality images and detailed descriptions. This helps customers make informed decisions and enhances their overall shopping experience.4. Offer Multiple Payment Options: Customized Bolt enables you to integrate multiple payment gateways, allowing customers to choose their preferred method of payment. By offering a variety of payment options, you can cater to different customer preferences and increase the likelihood of completing a purchase.5. Provide Social Proof: Social proof is a powerful marketing technique that can significantly influence consumer behavior. With Customized Bolt, you can incorporate customer reviews, ratings, and testimonials into your ecommerce platform. This provides potential customers with reassurance and confidence in your products, ultimately leading to higher conversion rates.In conclusion, optimizing your ecommerce experience is crucial for improving checkout conversion rates. With Customized Bolt, you can transform your website into a user-friendly, visually appealing, and personalized platform. By simplifying the checkout process, implementing a responsive design, enhancing product descriptions and images, offering multiple payment options, and providing social proof, you can create a seamless shopping experience that increases sales and keeps customers coming back for more. So, don't overlook the importance of ecommerce experience and start leveraging the power of Customized Bolt to take your online business to new heights.
Find Reliable Expansion Joints for Your Plant with Same or Next Day Delivery
Title: Understanding Flanged Rubber Expansion Joints: A Comprehensive GuideIntroduction:In industrial applications, ensuring the seamless operation and longevity of a plant is crucial. One often overlooked component that plays a critical role in this regard is the flanged rubber expansion joint. These flexible connectors are specifically designed to absorb movement, reduce vibration, and accommodate changes in pipe size, making them an indispensable part of any fluid handling system. In this blog, we will explore the fascinating world of flanged rubber expansion joints, their benefits, applications, and the factors to consider when choosing the right one for your project.Flanged Rubber Expansion Joints: Understanding the BasicsFlanged rubber expansion joints are precision-engineered connectors that provide the necessary flexibility to pipes and ductwork in various systems. They are comprised of reinforced rubber, fabric, or metal bellow sections, which allow for axial, lateral, and angular displacements. The primary function of these expansion joints is to compensate for thermal expansion, vibration, or movement caused by ground settlement or seismic activity. They also help in reducing noise transmission and absorbing shock to protect equipment and infrastructure.Benefits of Flanged Rubber Expansion Joints1. Flexibility and Movement Absorption: Flanged rubber expansion joints are designed to accommodate movement, angular deflection, and vibration. They act as a flexible link between pipe sections, absorbing both axial and lateral movements caused by thermal expansion or contraction, thereby preventing stress and damage to the system.2. Noise and Vibration Reduction: The rubber construction of these expansion joints helps in reducing noise transmission in the system, making them ideal for installations where noise control is critical. Additionally, they effectively dampen vibrations, preventing them from spreading throughout the system and causing potential damage.3. Corrosion Resistance: Flanged rubber expansion joints are resistant to a wide range of corrosive fluids, making them suitable for various industrial applications where the conveyed media may have corrosive properties. This property adds to their longevity and reduces maintenance costs.4. Fast Installation and Cost-Effectiveness: With various flange options available, these expansion joints can be easily fitted into existing or new piping systems. Their availability in stock and prompt delivery further ensures minimal downtime during installation or replacement.Applications of Flanged Rubber Expansion Joints1. HVAC Systems: Flanged rubber expansion joints are commonly used in heating, ventilation, and air conditioning (HVAC) systems to accommodate thermal expansion and vibration, ensuring the smooth operation of the system.2. Power Generation: Thermal power plants, nuclear power plants, and other energy generation facilities utilize flanged rubber expansion joints to absorb thermal expansion and protect critical components, such as pumps, turbines, and boilers.3. Chemical Processing: Flanged rubber expansion joints find extensive use in chemical processing plants, where they accommodate the corrosive nature of chemicals, compensate for thermal movement, and reduce vibration, ensuring safety and prolonged equipment life.4. Water and Wastewater Treatment: Municipal water treatment plants, sewage treatment facilities, and desalination plants all employ flanged rubber expansion joints to handle the constant movement of pipes due to temperature fluctuations and pressure changes, as well as to reduce noise and vibration.Choosing the Right Flanged Rubber Expansion JointWhen selecting a flanged rubber expansion joint for your specific application, several factors need to be considered:1. Operating Conditions: Ensure that the expansion joint is suitable for the temperature, pressure, and media conveyed in your system. This includes assessing the corrosiveness, abrasiveness, and the presence of any particulates in the fluid.2. Movement Capability: Determine the extent and type of movement (axial, lateral, angular) that may occur in the system, ensuring the expansion joint's design is capable of accommodating it.3. Flange Compatibility: Check that the flange design of the expansion joint matches that of the existing or adjoining pipes, ensuring a secure and leak-free connection.4. Size and Construction: Consider the size requirements, as well as the construction material of the expansion joint, to ensure it can withstand the demands of your specific application.Conclusion:Flanged rubber expansion joints are indispensable components of fluid handling systems, providing flexibility and accommodating the movements caused by thermal expansion, vibration, and ground settlement. Their ability to reduce noise, absorb shock, and resist corrosion makes them vital in ensuring the smooth operation and longevity of industrial plants. By considering the crucial factors discussed above, you can confidently choose the right flanged rubber expansion joint for your application, minimizing downtime, and optimizing safety.Remember, when it comes to the reliable and efficient operation of your plant, the appropriate choice of flanged rubber expansion joints is key.
Budget-Friendly Custom CNC Machine Parts for Durable Lathing Operations - Enquire Now!
Title: Custom CNC Lathing Parts - Delivering Durability on a BudgetIntroduction:Technological advancements have revolutionized the manufacturing industry, and CNC (Computer Numerical Control) machining has become an integral part of the production process. When it comes to developing precise, high-quality, and durable components, CNC lathing plays a crucial role. Among the many CNC lathing parts manufacturers, one company stands out - offering cost-effective solutions without compromising on quality.Understanding the Importance of CNC Lathing Parts:From aerospace and automotive industries to medical and electronics manufacturing, the demand for custom CNC machine parts continues to grow. CNC lathing refers to the process of shaping a workpiece using a rotating cutting tool, allowing for intricate designs and precision.Removing Brand Name - A Reliable Partner for Your CNC Lathing Part Needs:With years of experience and expertise, our company specializes in delivering custom CNC lathing parts to meet diverse industry requirements. We have established a reputation for delivering high-quality, durable components while maintaining affordability. Our commitment to customer satisfaction drives us to offer tailor-made solutions for every project.Aluminum CNC Lathing Parts - Exceptional Strength and Versatility:One of the primary materials used in CNC lathing parts is aluminum. Its outstanding properties include being lightweight, corrosion-resistant, and having excellent thermal conductivity. Aluminum CNC lathing parts find applications in various industries, ranging from automotive components to consumer electronics.The Process:Our team of skilled technicians and engineers utilizes state-of-the-art CNC machines to ensure precision and accuracy in the manufacturing process. We follow a meticulous approach that involves:1. Material Selection: Our experts carefully select the most suitable aluminum alloy based on the component's functionality, strength requirements, and environmental factors.2. CNC Programming: Utilizing computer-aided design (CAD) software, our engineers translate design specifications into machine-readable code. This step ensures precise replication of the desired component.3. Machining Process: The chosen aluminum alloy is mounted onto the CNC lathe, where the rotating cutting tool utilizes its precision to shape the workpiece according to the programmed design.4. Quality Assurance: Every CNC lathing part undergoes rigorous inspection to ensure its adherence to design specifications. Our quality control measures include dimensional checks, surface finish analysis, and mechanical strength testing.Benefits of Choosing Our Services:1. Cost-Effective Solutions: We understand the importance of keeping costs in check without compromising on quality. Our company offers affordable CNC lathing parts, making us the preferred partner for businesses operating on a budget.2. Tailor-Made Designs: Our dedicated team collaborates closely with clients to understand their specific requirements and design expectations. We pride ourselves on delivering custom CNC lathing parts that meet precise specifications.3. Reliable and Durable Components: Our focus on quality extends to the selection of materials, manufacturing processes, and rigorous inspections. We guarantee that our CNC lathing parts are built to withstand demanding environments and perform optimally.4. Timely Delivery: We value our customers' time and ensure that our products are delivered within agreed-upon timelines, maintaining efficient production schedules.Conclusion:In a highly competitive manufacturing landscape, it is essential to choose a CNC lathing parts manufacturer that offers durable and high-quality components without breaking the bank. Our company delivers cost-effective solutions, specializing in aluminum CNC lathing parts that meet stringent industry standards. With a focus on customer satisfaction, precision machining, and timely delivery, we are the reliable partner you can count on for your CNC lathing part needs. Reach out to us today for a personalized consultation or an estimate that aligns with your project requirements.
Flange facts - An external or internal rib or rim, typically found on iron beams, I-beams, or T-beams, providing added strength. Factolex offers a concise lexicon of terms, focusing on delivering straightforward information to users. Facts are arranged based on their relevance within the community, allowing you to create your personalized lexicon. Additionally, we can optimize the SEO title by removing the brand name.
Web And Flange Of T Beam: Crucial Components of Structural Stability and StrengthIn the realm of structural engineering, the proper design and construction of beams play a pivotal role in ensuring the stability and strength of various structures. One such type of beam that is widely used in construction projects is the T-beam, known for its distinctive shape resembling the letter "T". The T-beam consists of two main components, namely the web and flange, which work in tandem to provide the necessary structural support and strength. This article delves into the significance of the web and flange of a T-beam, highlighting their key features and functions.The web is the vertical component of the T-beam, connecting the top and bottom flanges. It serves as the main load-bearing element, resisting the bending forces exerted on the beam. Typically, the web is designed to be thin but wide, as it primarily acts in tension and compression, rather than bending. The width of the web is determined by factors such as the load and span of the beam, as well as the type of material used. Reinforcing bars, known as stirrups, are often added diagonally across the web to enhance its resistance against shear forces.On the other hand, the flange of a T-beam is the horizontal component that extends perpendicularly from the web. It plays a crucial role in providing additional support and strength to the beam, distributing the load evenly throughout the structure. The top flange is commonly subjected to compression forces, while the bottom flange experiences tension forces. The dimensions of the flanges are determined by factors such as the load and span of the beam, as well as the material used. Additionally, flanges are often reinforced with steel bars or plates to enhance their load-bearing capacity.The combination of the web and flange in a T-beam results in a structure that can efficiently withstand various types of loads, including dead loads (e.g., the weight of the structure itself), live loads (e.g., the weight of people or objects), and dynamic loads (e.g., wind or seismic forces). By distributing the load over a larger area, the T-beam can handle significant amounts of weight without deformation or failure. This makes it a popular choice for the construction of bridges, buildings, and other structures where strength and stability are paramount.It is important to note that the design and construction of T-beams require careful consideration of several factors. These include the intended use of the structure, the anticipated loads, the span of the beam, the properties of the materials, and the applicable building codes and regulations. Structural engineers play a crucial role in analyzing these factors and determining the appropriate dimensions and reinforcement requirements for the web and flange. By adhering to industry standards and best practices, they ensure that the T-beam meets the necessary safety and performance criteria.In conclusion, the web and flange are essential components of a T-beam, working together to provide the necessary structural support and strength. The web acts as the primary load-bearing element, while the flange distributes the load and enhances the beam's capacity to withstand various forces. The proper design and construction of these components are crucial to ensure the stability and integrity of structures such as bridges and buildings. By understanding the significance of the web and flange in a T-beam, engineers can confidently design and construct robust and reliable structures.