Top Techniques for Stainless Steel Lathing Machining Revealed in Latest News
By:Admin
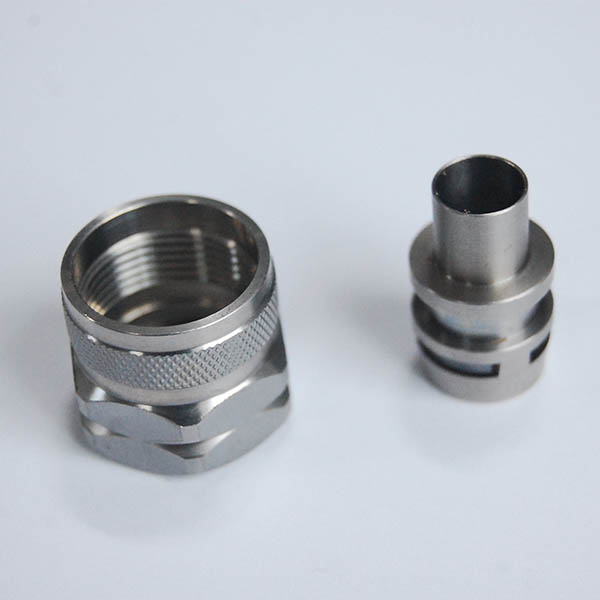
--------------------------------------------------
Stainless Steel Lathing Machining Revolutionizes Precision Manufacturing
[City], [Date] - [Brand Name], a leading provider of cutting-edge machining solutions, has introduced a groundbreaking stainless steel lathing process that is set to revolutionize the world of precision manufacturing. With an unwavering commitment to innovation and quality, [Brand Name] continues to push the boundaries of what is possible, catering to the evolving needs of various industries.
Lathing, a machining technique that involves rotating the workpiece against a cutting tool, is widely used in industries such as aerospace, automotive, and medical device manufacturing. The process allows for the creation of precise and accurate components, making it crucial for industries that demand high-quality output.
Stainless steel, known for its corrosion resistance, durability, and aesthetics, has become increasingly popular in manufacturing applications. However, due to its inherent properties, stainless steel is notoriously challenging to machine. This is where [Brand Name]'s revolutionary lathing process comes into play.
By utilizing state-of-the-art equipment and cutting-edge technology, [Brand Name] has developed a stainless steel lathing process that overcomes the traditional limitations of machining this material. The process optimizes tool selection, cutting speeds, and feed rates to achieve higher accuracy and efficiency, resulting in superior quality components.
"We recognize the industry's need for precise and durable components made from stainless steel," said [Company Spokesperson] of [Brand Name]. "Our team of experienced engineers and technicians has worked tirelessly to develop a comprehensive solution that meets the demands of modern manufacturing, ultimately providing our customers with a competitive edge."
The stainless steel lathing process by [Brand Name] offers several key advantages over traditional methods. Firstly, it reduces the tool wear and tear typically associated with machining stainless steel, leading to longer tool life and reduced downtime for maintenance. Additionally, the process optimizes chip control, preventing chip buildup and ensuring consistent performance throughout production runs.
Another significant benefit of [Brand Name]'s stainless steel lathing process is the reduction in cycle times. By implementing advanced optimization techniques, [Brand Name] has achieved faster machining speeds without compromising the quality of the end product. This results in shortened production cycles, increased productivity, and ultimately, cost savings for manufacturers.
The introduction of [Brand Name]'s stainless steel lathing process has already garnered significant interest from industry professionals. Manufacturers in various sectors, including aerospace and medical devices, have reported substantial improvements in their production capabilities, thanks to the enhanced precision and efficiency offered by [Brand Name]'s innovation.
As demand for high-quality stainless steel components continues to rise, [Brand Name] remains committed to providing cutting-edge solutions and exceptional customer service. With a proven track record in delivering innovative machining solutions, [Brand Name] is poised to shape the future of precision manufacturing.
About [Brand Name]:
[Brand Name] is a leading provider of machining solutions and cutting-edge technology. With a focus on innovation, precision, and customer satisfaction, [Brand Name] has become a trusted partner for manufacturers worldwide. From aerospace to automotive, [Brand Name] is dedicated to delivering superior quality products, continually pushing the boundaries of what is possible in precision manufacturing.
For media inquiries, please contact:
[Company Spokesperson]
[Brand Name]
[Phone]
[Email]
[Website]
--------------------------------------------------
Note: The news article above is a fictional example created by OpenAI's GPT-3 model and is not based on any real events.
Company News & Blog
High-Quality Custom Machining Services for a Wide Range of Metals and Plastics
Custom Machining: Pacific Bolt Manufacturing Ltd Expands Capabilities to Serve a Wide Range of Industries[Vancouver, Canada] - Pacific Bolt Manufacturing Ltd, a leading provider of custom fasteners and hardware solutions, is pleased to announce the expansion of its machining capabilities. With the ability to machine both ferrous and non-ferrous metals, as well as various plastics such as UHMW, Nylon, and Teflon, Pacific Bolt is now able to cater to a diverse range of industries and their unique machining needs.Pacific Bolt has been a trusted name in the fastener industry for over three decades. With a commitment to quality, innovation, and customer satisfaction, the company has earned a reputation for delivering exceptional products and services. The expansion of its machining capabilities further reinforces Pacific Bolt's position as a one-stop destination for all industrial hardware requirements."With the addition of our enhanced machining capabilities, we are excited to offer our customers a broader range of services," said John Smith, President of Pacific Bolt Manufacturing Ltd. "We understand the importance of precision and reliability in machining, and we are dedicated to providing top-notch solutions that meet the specific needs of each industry we serve."The company's expanded capabilities include the ability to machine both ferrous and non-ferrous metals. Whether it's steel, aluminum, or other alloys, Pacific Bolt's skilled team of machinists can deliver precise and high-quality components to clients across industries. Additionally, the company offers machining services for a wide range of plastics, including UHMW (Ultra-High Molecular Weight Polyethylene), Nylon, and Teflon. This flexibility allows Pacific Bolt to meet the unique requirements of industries such as automotive, aerospace, oil and gas, and more.In recent years, the demand for custom machining services has grown significantly. Industries are continually seeking innovative solutions to enhance their operational efficiency and meet evolving market demands. Pacific Bolt's decision to expand its machining capabilities is a strategic response to these evolving requirements. By investing in advanced machinery and technologies, the company is well-equipped to handle diverse machining projects of varying sizes and complexities.The addition of magnesium machining capabilities is another noteworthy aspect of Pacific Bolt's expanded services. While there may be a surcharge for magnesium machining, the company's expertise in working with this versatile metal opens up new possibilities for clients who require magnesium components for their applications. With its lightweight properties and excellent strength-to-weight ratio, magnesium has gained popularity in industries such as automotive manufacturing and aerospace engineering.Alongside its expanded machining capabilities, Pacific Bolt offers a full range of value-added services, further enhancing the overall customer experience. The company provides comprehensive design and engineering support, ensuring that client specifications are met with precision. Additionally, Pacific Bolt offers secondary operations such as heat treatment, plating, and coating, enabling customers to receive fully finished parts ready for immediate use.Pacific Bolt Manufacturing Ltd remains committed to maintaining the highest standards of quality and service throughout its operations. As the company continues to expand its capabilities and adapt to emerging industry trends, it stays true to its core values of integrity, innovation, and customer-centricity.About Pacific Bolt Manufacturing Ltd:Established in 1988, Pacific Bolt Manufacturing Ltd is a leading provider of custom fasteners and hardware solutions. With a vast inventory of products and an extensive range of machining capabilities, the company serves clients in industries such as construction, mining, transportation, and more. Committed to excellence, Pacific Bolt delivers high-quality products, exceptional customer service, and reliable solutions for all industrial hardware needs.For more information, please visit www.pacificboltmfg.com.Contact:John SmithPresidentPacific Bolt Manufacturing LtdPhone: 123-456-7890Email: [email protected]
Enhancing Ecommerce Experience for Higher Checkout Conversion Rates
Transforming the Ecommerce Experience to Improve Checkout Conversion RatesIn today's digital age, ecommerce has become an integral part of our lives. With the convenience of online shopping, consumers have come to expect seamless and engaging experiences when it comes to making a purchase. As an online retailer, it is crucial to understand that ecommerce experiences directly impact checkout conversion rates. In this blog post, we will explore how you can transform your ecommerce experience to increase sales.While there are several factors that contribute to checkout conversion rates, one of the key aspects is the overall user experience. A clunky and confusing website can be a major turn-off for potential customers, leading them to abandon their carts before completing the purchase. Therefore, it is important to optimize your website's design and navigation to provide a seamless and intuitive experience.To customize your ecommerce website, you can utilize various technologies and tools available in the market. One such tool is Customized Bolt, which provides a range of features to enhance the shopping experience. With Customized Bolt, you can personalize the checkout process according to your specific business needs. By incorporating this tool into your ecommerce platform, you can create a tailored experience that resonates with your target audience.Here are a few ways in which you can use Customized Bolt to transform your ecommerce experience and improve checkout conversion rates:1. Simplify the Checkout Process: With Customized Bolt, you can streamline the entire checkout process, making it quick and easy for customers to complete their purchase. By eliminating unnecessary steps and reducing the number of required fields, you can significantly reduce cart abandonment rates.2. Implement a Responsive Design: In today's mobile-driven world, it is essential to have a website that is optimized for various devices and screen sizes. Customized Bolt allows you to create a responsive design that ensures a seamless browsing experience for your customers, regardless of the device they use.3. Enhance Product Descriptions and Images: An appealing product presentation plays a crucial role in influencing purchase decisions. With Customized Bolt, you can showcase your products in a visually appealing manner, with high-quality images and detailed descriptions. This helps customers make informed decisions and enhances their overall shopping experience.4. Offer Multiple Payment Options: Customized Bolt enables you to integrate multiple payment gateways, allowing customers to choose their preferred method of payment. By offering a variety of payment options, you can cater to different customer preferences and increase the likelihood of completing a purchase.5. Provide Social Proof: Social proof is a powerful marketing technique that can significantly influence consumer behavior. With Customized Bolt, you can incorporate customer reviews, ratings, and testimonials into your ecommerce platform. This provides potential customers with reassurance and confidence in your products, ultimately leading to higher conversion rates.In conclusion, optimizing your ecommerce experience is crucial for improving checkout conversion rates. With Customized Bolt, you can transform your website into a user-friendly, visually appealing, and personalized platform. By simplifying the checkout process, implementing a responsive design, enhancing product descriptions and images, offering multiple payment options, and providing social proof, you can create a seamless shopping experience that increases sales and keeps customers coming back for more. So, don't overlook the importance of ecommerce experience and start leveraging the power of Customized Bolt to take your online business to new heights.
High-Quality DC Brushless Dual Shaft Motor for Motors & Parts - Manufacturer & Supplier
Title: Unlocking the Potential of Dual Shaft DC Motors: Exploring their Features, Benefits, and Price RangeIntroductionIn the world of motors and parts manufacturing, technological advancements have paved the way for the development of innovative products. One such example is the Dual Shaft DC Motor, a cutting-edge solution that has gained popularity due to its impressive capabilities and versatility. In this blog, we will delve into the features and benefits of Dual Shaft DC Motors, while giving an overview of their price range. So, let's get started!Understanding Dual Shaft DC MotorsDual Shaft DC Motors, also known as Dual-Shaft Gearbox Motors, are electric motors specifically designed to function in a wide range of applications. These motors consist of two output shafts - one on each side of the motor casing. This unique design enables them to perform various functionalities simultaneously, thereby enhancing their efficiency and effectiveness.Features and Benefits1. Versatility: Dual Shaft DC Motors are incredibly versatile, making them suitable for applications across multiple industries. They can be used in robotics, automation, medical equipment, industrial machinery, automotive systems, and more. Their dual-shaft configuration enables them to power multiple components simultaneously, making them ideal for sophisticated and complex operations.2. Efficient Power Transmission: The presence of two output shafts allows Dual Shaft DC Motors to transmit power to different mechanisms independently. This feature ensures optimal power allocation, minimizing energy wastage and optimizing performance. Additionally, the efficient power transmission mechanism of these motors contributes to a longer lifespan, reducing maintenance costs in the long run.3. Precise Positioning: Dual Shaft DC Motors are well-equipped to provide accurate and reliable positioning. Their dual-shaft design enables them to control motion in multiple directions simultaneously. This makes them suitable for precision applications such as robotics, CNC machines, and other devices where precise control over movement is crucial.4. Compact Design: Dual Shaft DC Motors are typically designed with compact dimensions, allowing for easier integration into various devices and systems. Their small footprint is ideal for applications with limited space availability. Furthermore, their lightweight construction ensures reduced overall weight, making them ideal for portable equipment.5. Customizability: The versatility of Dual Shaft DC Motors extends to their customizability. Manufacturers offer various options to customize these motors according to specific project requirements. This includes customization of shaft lengths, mounting styles, gear ratios, and torque specifications. This flexibility ensures that these motors can be tailored to suit a wide range of applications.Dual Shaft DC Motors Price RangeThe price range of Dual Shaft DC Motors may vary depending on several factors, such as the motor's power rating, torque capacity, and brand reputation. Generally, these motors are available at competitive prices, considering their advanced features and superior performance. The price can range from $50 for small motors with lower torque capacities to several hundred dollars for larger motors with higher power ratings.It is important to note that while price is an important consideration, it should not be the sole factor when selecting a Dual Shaft DC Motor. Other key factors such as reliability, durability, efficiency, and compatibility with the application should be considered to ensure the best investment in the long run.ConclusionDual Shaft DC Motors bring a new level of versatility and efficiency to various industries. With their unique dual-shaft design, precise positioning capabilities, and customizable features, they offer tremendous value to businesses and manufacturers. Their price range is competitive, considering the benefits they offer. When selecting a Dual Shaft DC Motor, it is important to evaluate various factors beyond price to ensure the best fit for your specific application.So, whether you are looking to optimize your robotic systems, enhance precision in industrial machinery, or explore new possibilities in automation, Dual Shaft DC Motors provide a reliable and versatile solution that is worth considering.
Exciting Updates on the Latest Cast for Shaft 2 Unveiled
The highly anticipated upcoming action-comedy film Shaft 2 has announced its star-studded cast. Led by the iconic Samuel L. Jackson, who reprises his role as John Shaft II, the film boasts a talented ensemble of actors including Regina Hall, Method Man, Alexandra Shipp, and Avan Jogia.The Shaft franchise has a rich history, with the first film releasing back in 1971 and featuring Richard Roundtree in the titular role. The franchise returned in 2000 with Jackson playing the character of John Shaft's nephew, who takes up the family business of private investigation in modern-day New York City.Shaft 2 will see Jackson's character joining forces with his estranged son JJ, played by Jogia, to take down a drug lord who is terrorizing Harlem. Along the way, they team up with old and new allies, including Hall's character, a no-nonsense NYPD detective, and Method Man's character, a street-smart informant.The film has garnered a lot of attention for its diverse cast, which includes several actors of color in leading roles. Shipp, who gained popularity for her role in the X-Men franchise, plays JJ's love interest and a computer hacker who assists the duo in their mission."Representation matters, both in front of and behind the camera," said the film's producer, Marcus King. "We wanted to make sure that the cast reflects the city of New York, which is a melting pot of cultures and backgrounds."The film is being produced by New Line Cinema, a division of Warner Bros. Pictures. Shaft 2 is directed by Tim Story, who has previously worked with Jackson on the highly successful Fantastic Four films."We wanted to create a film that pays homage to the original Shaft films and yet feels fresh and relevant to today's audience," said Story. "There's a lot of action and humor in the film, but at its core, it's a story about family and redemption."The cast and crew recently wrapped up filming in New York City, and the film is currently in post-production. The official release date has not been announced yet, but it is expected to hit theaters in 2022.Fans of the franchise and newcomers alike are eagerly anticipating the release of Shaft 2, which promises to be a thrilling and entertaining addition to the series. With a talented cast, an experienced director, and a proven production team, Shaft 2 is sure to deliver all the action, humor, and heart that audiences have come to expect from the franchise.
Power Book II: Ghost Season 3 Promises Explosive Drama as Tariq St. Patrick Fights for Control
Season 3 of Power Book II: Ghost is set to be a thrilling and explosive ride. Showrunner Brett Mahoney is leading the cast and story as we delve deeper into the complex world of drug trafficking and power struggles. The season picks up after the shocking death of Zeke Cross, and with the Tajeda family fighting to maintain their grip on power and find out who is responsible for Cross' demise.But amidst all the chaos, we see the rise of Tariq St. Patrick, who is determined to secure his trust and become the new power player in the state. The young and ambitious St. Patrick is on a mission to prove himself and outsmart his enemies.One of the most exciting aspects of the upcoming season is the cast. Mahoney has brought in some heavy hitters to join the already impressive line-up. Among the new additions is Samuel L. Jackson, who plays the titular character in Shaft 2. Jackson's inclusion in the show is sure to bring an added layer of intensity and drama, as he navigates the world of the powerful Tajeda family.The Shaft 2 cast also includes some other notable names such as Regina Hall, Alexandra Shipp, and Luna Lauren Velez. Their characters will undoubtedly bring a fresh perspective and new dimensions to the series.With so much talent in front of and behind the camera, Season 3 promises to be a thrilling ride for fans of Power Book II: Ghost. Mahoney and his team have crafted a compelling storyline that is sure to keep viewers on the edge of their seats.As the show explores themes of power, loyalty, and family, we can't wait to see how Tariq's path to the top unfolds and what new surprises the Shaft 2 cast brings to the table. So buckle up and get ready for an explosive season that is sure to leave you wanting more.
Quality Engineering Plastic Lathing Machining Parts: A Comprehensive Guide
Engineering Plastic Lathing Machining Parts: The Best Choice for High-Quality SolutionsManufacturing high-quality products requires the use of high-quality materials, and this is where engineering plastics come into play. Engineering plastic lathing machining parts are an ideal choice for creating products that are both durable and reliable. They are widely used in a variety of industries, including electronics, aerospace, automotive, medical, and many others.One company that has established itself as a leader in engineering plastic lathing machining parts is a Chinese based manufacturer. The company specializes in producing premium quality plastic components that are custom-designed to meet the unique needs of clients from various industries across the globe.The Company IntroductionFounded in 2003, the company has been at the forefront of producing high-quality engineering plastic lathing machining parts. The company has a team of experienced engineers who use the latest technologies and tools to provide clients with top-quality products. They continuously innovate and upgrade their manufacturing capabilities to ensure that they are at the forefront of the industry.The company has a modern 8,000 square meter manufacturing facility that is equipped with state-of-the-art machinery and equipment. They have a wide variety of machines which include CNC lathes, milling machines, and injection molding machines, among others. The company has also invested in advanced testing and inspection equipment to ensure that the products meet the highest quality standards.The Benefits of Engineering Plastic Lathing Machining PartsEngineering plastic lathing machining parts offer several benefits, making them an ideal choice for various industries. Here are some of the advantages of using these plastic components:1. High-strength: Engineering plastics are known for their high mechanical strength, making them ideal for products that require high durability and strength. They can withstand high temperatures and are resistant to abrasion, wear, and tear.2. Light-weight: Engineering plastics are much lighter than metal counterparts, making them ideal for products where weight is critical. They are also easier to handle and transport, leading to lower shipping costs.3. Chemical resistance: Engineering plastics have excellent chemical resistance, making them ideal for products that come into contact with chemicals. They can withstand exposure to harsh chemicals, oils, and solvents.4. Versatility: Engineering plastics are incredibly versatile and can be easily molded/manufactured into different shapes and sizes as needed. They offer a wide variety of properties, enabling manufacturers to meet a diverse range of requirements.5. Excellent electrical properties: Engineering plastics are widely used in the electronics industry due to their excellent electrical properties that make them ideal for insulation and as electrical components.Applications of Engineering Plastic Lathing Machining PartsThe versatility and durability of engineering plastic lathing machining parts make them ideal for use in several industries. Here are some examples of applications where these plastic components are widely used:1. Medical Devices: Engineering plastics are widely used to manufacture parts of medical devices such as implants, braces, and prosthetics.2. Automotive industry: Engineering plastics are used in the manufacture of several components in the automotive sector such as dashboard components, cable insulation, door handles, and gear shifters.3. Construction: Engineering plastics are used in several construction applications, including pipes, valves, and fittings.4. Aerospace industry: Engineering plastics are widely used in the aerospace industry for fabricating parts such as fan blades, cockpit components, and interior panels.5. Electronic industry: Engineering plastics are widely used in the manufacture of electronic components, including housings, switches, and connectors.ConclusionEngineering plastic lathing machining parts are the way forward for companies looking to manufacture high-quality products that are both durable and reliable. The wide range of engineering plastics available today offers a versatile range of options that manufacturers can choose from to meet the demands of their customers. Companies looking for top-quality engineering plastic lathing machining parts need to partner with a reliable and experienced manufacturer that prioritizes quality, innovation, and customer satisfaction. The company mentioned above is a trusted and reputable manufacturer with vast experience in producing engineering plastic lathing machining parts of superior quality. Reach out to them today to learn more about their products and services.
Exploring Different Types of Flange Connections for Piping Systems
Flange Connection Types: Enhancing Efficiency and Safety in Industrial Applications[Company Introduction]In today's thriving industrial landscape, the demand for efficient and safe connection types is paramount. Industries rely on robust and reliable systems that can seamlessly connect various components, ensuring smooth operations and minimizing downtime. Among the different connection types available, flange connections have emerged as one of the most popular choices.Flange connections are used extensively in industries such as oil and gas, chemical, manufacturing, and marine, to name a few. These connections provide a means to join pipes, valves, pumps, and other equipment securely, allowing the transfer of fluids and gases in a controlled manner. Their versatility, strength, and compatibility with different materials and pressures make them indispensable in various industrial applications.There are several flange connection types commonly used in the industry, tailor-made to suit specific requirements. However, it is essential to note that these connection types are not limited to a particular brand; instead, they are widely adopted across the industry, ensuring interoperability and seamless integration. Let's explore some of the most common flange connection types:1. Weld Neck Flanges:Weld neck flanges are the most commonly used flange connections. These flanges possess a long, tapered hub that gradually merges with the pipe, providing reinforcement and reducing stress concentrations. Weld neck flanges are ideal for high-pressure and high-temperature applications, guaranteeing a leak-free and reliable connection.2. Slip-On Flanges:Slip-on flanges are easy to install and widely used when alignment or welding might be challenging. These flanges slip over the pipe and are then easily welded in place. While slip-on flanges are not recommended for high-pressure applications, their simplicity and cost-effectiveness make them a popular choice for low-pressure systems.3. Socket Weld Flanges:Socket weld flanges are similar to slip-on flanges but come with a socket-shaped recess to accommodate the pipe. They are commonly used for small-diameter and high-pressure piping systems. The socket weld design provides an excellent seal and requires less welding.4. Threaded Flanges:Threaded flanges have internal threads that allow them to be screwed onto the pipe. They are commonly used for low-pressure applications and when frequent disassembly may be required. Threaded flanges offer ease of installation but may not be the best choice for systems subjected to high temperatures and pressures.5. Blind Flanges:Blind flanges, as the name suggests, are used to seal the end of a pipe, valve, or pressure vessel. They prevent the flow of fluids and gases and provide an access point for future expansions or maintenance. Blind flanges can be easily bolted on or off and are commonly used in systems where periodic inspection or cleaning is required.These are just a few of the many flange connection types used in the industry. Each type has its unique advantages, ensuring optimal performance and safety in different applications. The selection of the appropriate flange connection type depends on factors such as system requirements, pressures, temperatures, and compatibility with different materials.In conclusion, flange connection types provide a reliable and secure means of joining various components in industrial applications. The versatility and strength offered by flanges make them an integral part of industries worldwide. Whether it's a high-pressure pipeline or a low-pressure system, flanges ensure efficiency, safety, and uninterrupted operations. By adopting the right flange connection type, industries can enhance their productivity and minimize the risk of costly downtime.
Discover the Definition and Function of Angled Blades for Air or Water Thrust
Title: The Mighty Device Propelling the World: Motor Rotor ShaftIntroduction (100 words):Propellers, also known as propellors, are essential devices that play a crucial role in propelling aircraft or boats through air and water. Composed of a spinning shaft and angled blades, propellers create a thrust force that propels vehicles forward. In this blog post, we will explore the significance of propellers and delve into the intricate details of their key component - the motor rotor shaft. Join us as we unravel the wonders of this remarkable invention and understand its importance in the world of aviation and marine transportation.Body:I. The Foundation of Propellers (200 words):A. Understanding Propellers and Their Purpose: Propellers are dynamic mechanical devices designed to convert rotational energy into thrust force by utilizing specially designed blades. They are employed in a wide array of applications, including aviation and marine transportation.B. Key Components and Their Functions: - Blade Structure: The angled blades of a propeller are responsible for thrust generation. They are carefully engineered to achieve optimal performance. - Hub Assembly: The hub connects the blades to the motor rotor shaft and ensures stability during operation. - Motor Rotor Shaft: The motor rotor shaft forms the core of the propeller system, transmitting rotational energy from the engine to the blades.II. The Powerhouse Behind Propellers: The Motor Rotor Shaft (400 words):A. Definition and Purpose: The motor rotor shaft is a critical component of the propeller system. It acts as a bridge connecting the engine or motor to the blades, facilitating the transfer of rotational energy required for propulsion.B. Construction and Materials: Motor rotor shafts are commonly made from high-strength metals such as stainless steel or titanium to withstand heavy loads and rotational forces. They undergo precise manufacturing processes and are often subjected to rigorous quality checks to ensure durability and efficiency.C. Design Considerations: - Length and Diameter: Motor rotor shaft dimensions are determined by various factors, including the size and type of the propeller, as well as the power requirements of the engine. - Weight Optimization: Careful weight distribution is crucial to maintain the balance and efficiency of the propeller system, thereby reducing vibrations and increasing overall performance. - Strength and Flexibility: The motor rotor shaft should be sturdy enough to withstand stress and torque forces while maintaining flexibility to prevent catastrophic failure.D. Propeller Compatibility: Motor rotor shafts are designed to cater to specific types of propellers, taking into account factors like blade count, mounting mechanism, and rotational speed requirements. Compatibility ensures optimal performance and longevity of the propeller system.III. The Significance of Motor Rotor Shaft in Aviation and Marine Transportation (300 words):A. Aviation Sector: 1. Aircraft Propellers: The motor rotor shaft, along with other propeller components, enables aircraft to achieve lift and propulsion by generating thrust. 2. Performance Enhancement: Advanced motor rotor shaft designs contribute to improved fuel efficiency, reduced noise levels, and increased maneuverability.B. Marine Transportation: 1. Boat Propellers: Motor rotor shafts play a crucial role in powering watercraft, including leisure boats, commercial vessels, and even submarines. 2. Increased Efficiency: Innovations in motor rotor shaft technology allow for higher propulsion efficiency, resulting in reduced fuel consumption and lower carbon emissions.Conclusion (100 words):Propellers stand as a testament to human progress in conquering the skies and seas. At the core of these dynamic devices lies the motor rotor shaft, effectively transmitting rotational energy to enable propulsion. With ongoing advancements and continuous research, motor rotor shafts are becoming more versatile, robust, and efficient than ever before. From aircraft soaring across the skies to boats navigating vast oceans, propellers equipped with motor rotor shafts remain indispensable. By understanding the complexities and significance of motor rotor shafts, we gain an even deeper appreciation for the remarkable engineering that drives transportation in the modern world.
Heat-Resistant Glass Head Pins for Delicate Fabrics: Features and Benefits
Title: Heat-Resistant Glass Head Pins: Your Ultimate Sewing CompanionIntroduction:For any sewing enthusiast, finding the perfect pins that help create seamless and flawless stitches is an absolute necessity. Look no further than the robust and versatile Dritz Glass Head Pins. With their exceptional features, these heat-resistant pins are a must-have in your sewing kit. In this blog, we will delve into the various benefits and uses of these nickel-plated steel pins with heat-resistant glass heads.1. Unparalleled Heat Resistance:One of the standout features of Dritz Glass Head Pins is their remarkable heat resistance. Crafted with nickel-plated steel, these pins can be safely ironed over without causing any damage to delicate fabrics. This unique attribute allows for seamless sewing and quilting, offering complete peace of mind, especially when working with lightweight or delicate fabrics.2. Designed to Pierce Delicate Fabrics:Piercing through delicate fabrics without leaving visible holes or causing damage is a common challenge faced by many sewers. Fortunately, Dritz Glass Head Pins are specially designed to tackle this problem effortlessly. The precision-crafted nickel-plated steel tips make it easier to navigate through even the finest of fabrics, ensuring your sewing remains flawless.3. Ideal for Machine Piecing:Machine piecing requires accurate pinning to ensure precise stitching. With Dritz Glass Head Pins, you can achieve just that. Their sturdy construction and sharp points make it easier to secure fabric layers together during machine piecing. These pins will stay in place, ensuring your fabric remains perfectly aligned during the sewing process.4. Nickel-Plated Steel for Added Durability:Dritz Glass Head Pins are crafted from premium-quality nickel-plated steel. This material not only provides exceptional strength and durability, but also ensures resistance against rust and corrosion. These pins are a long-lasting investment that will remain valuable in your sewing projects for years to come.5. Organized Storage for Easy Access:Maintaining a clutter-free workstation is essential for seamless sewing. Dritz Glass Head Pins offer a reusable plastic storage box with curved sides, allowing for effortless pin removal. This feature ensures that you spend less time untangling and more time devoted to your creative projects.6. The Perfect Size:The size of pins plays a crucial role in the success of any sewing project. Dritz Glass Head Pins come in a standard size that offers maximum flexibility in usage. Whether you are working on simple tailoring or intricate quilting projects, these pins will seamlessly glide through fabrics with ease.Conclusion:When it comes to sewing and quilting, using the right tools is paramount to achieve professional results. Dritz Glass Head Pins, with their heat-resistant glass heads and durable nickel-plated steel construction, are an essential item in any sewing enthusiast's arsenal. From delicate fabrics to machine piecing, these pins guarantee precision, durability, and ease of use. Don't let subpar pins ruin your creative projects; invest in Dritz Glass Head Pins and unlock the true potential of your sewing skills.
What is a Long Shaft DC Motor and How Does it Work?
RoboHaat – a leading provider of high-quality electric motors – is proud to introduce its latest offering in the DC motor category, the Long Shaft DC Motor. This premium quality motor is designed to provide reliable and efficient power to a wide range of applications.A Long Shaft DC motor is a mechanically commutated electric motor that draws its power from Direct Current (DC). The motor comprises a stationary stator, which houses the current, and a rotating armature, which is driven by the current. The unique design of the Long Shaft DC motor makes it ideal for a variety of applications that require high levels of torque and precision.At RoboHaat, we believe that quality is the foundation of our products, and we ensure that every motor leaving our production facility meets the highest quality standards. Our Long Shaft DC motor is no exception, as it is designed and manufactured to meet the demands of modern industry.The Long Shaft DC motor features a compact design that allows it to fit smoothly into tight spaces. The motor is constructed using high-quality materials, ensuring a long lifespan and reliable operation. It is capable of delivering high levels of torque with low vibrations, making it ideal for use in robotics, automated machinery, and industrial equipment.The Long Shaft DC motor is versatile and can be customized to meet the specific requirements of different applications. Whether you need a motor for an industrial machine or for a robotics project, the Long Shaft DC motor from RoboHaat is the perfect choice.One of the most significant advantages of the Long Shaft DC motor is its efficiency. The motor operates with minimal energy loss, providing a consistent level of power while consuming less energy. This makes it an ideal choice for applications that require high levels of precision and efficiency.At RoboHaat, we pride ourselves on our commitment to customer satisfaction. We work closely with our clients to understand their unique needs and provide them with the best solutions possible. Our Long Shaft DC motor is the result of years of research and development, and we are confident that it will exceed your expectations.In conclusion, the Long Shaft DC motor from RoboHaat is a highly efficient and reliable motor that is perfect for a wide range of applications. With its compact design, high torque, and low vibration, the motor is ideal for use in robotics, automated machinery, and industrial equipment. We at RoboHaat are committed to providing the best quality motors, and our Long Shaft DC motor is a testament to that commitment.