Top 5 Tips for Choosing a High-Quality Machining Factory
By:Admin
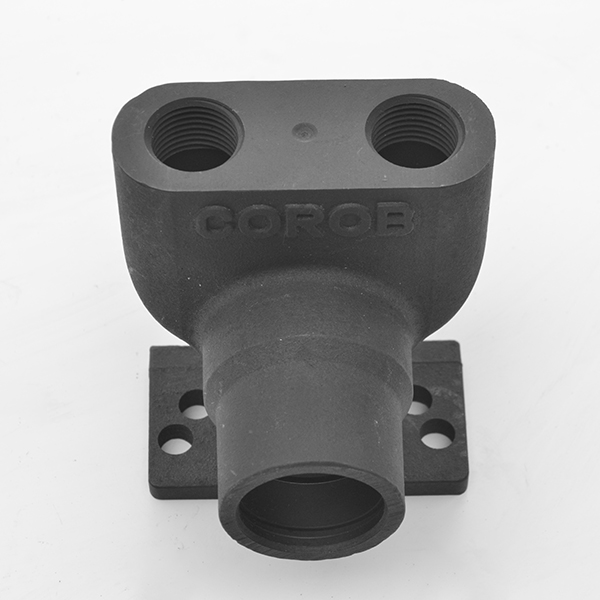
The company's state-of-the-art facility is equipped with the latest machinery and equipment, allowing them to produce high-quality, precision-engineered products for a wide range of industries. The factory's skilled and experienced workforce is dedicated to delivering superior results, consistently meeting and exceeding customer expectations.
Machining Factory has built a reputation for its exceptional customer service and a strong focus on innovation and continuous improvement. The company is committed to staying ahead of the competition by investing in research and development, exploring new technologies, and fostering a culture of creativity and collaboration.
The company offers a comprehensive range of machining services, including CNC milling, turning, grinding, and more. Their capabilities cover a broad spectrum of materials, from metals to plastics, and they have the expertise to handle complex and intricate projects with precision and efficiency.
One of the key factors behind Machining Factory's success is its dedication to quality management and assurance. The company adheres to strict quality control processes at every stage of production, ensuring that every product that leaves the factory meets the highest standards of quality and reliability.
In addition to its focus on quality, the company is also committed to sustainability and environmental responsibility. Machining Factory has implemented eco-friendly practices and initiatives to minimize its impact on the environment, demonstrating a strong sense of corporate social responsibility.
With a strong track record of delivering superior products and services, Machining Factory has earned the trust and loyalty of its customers, who rely on the company for their machining needs. From small-scale components to large-scale production runs, Machining Factory has the expertise and resources to handle projects of any size and complexity.
The company's commitment to excellence has earned it accolades and recognition in the industry, solidifying its position as a leader in the market. Machining Factory continues to evolve and adapt to the changing needs of its customers, embracing new technologies and methodologies to stay ahead of the curve.
As the manufacturing and machining industry continues to evolve, Machining Factory remains at the forefront, setting the standard for quality, innovation, and customer satisfaction. The company's dedication to excellence and its relentless pursuit of improvement make it a force to be reckoned with in the market.
In conclusion, Machining Factory is a powerhouse in the manufacturing and machining industry, with a strong reputation for quality, innovation, and customer satisfaction. With its advanced technology, skilled workforce, and commitment to excellence, the company is poised to continue its upward trajectory and maintain its position as a leader in the market.
Company News & Blog
Custom CNC Machining Manufacturer: Leading the Industry in Precision Manufacturing
CNC Machining Manufacturer Leads Innovation in Precision ManufacturingIn the world of precision manufacturing, CNC machining has become an essential tool for producing high-quality components with tight tolerances. One company that has been leading the way in this field is {Company}, a renowned CNC machining manufacturer that has been setting the standard for precision and innovation.Established in {Year}, {Company} has built a reputation for excellence in CNC machining, offering a wide range of services including milling, turning, drilling, and grinding. The company's state-of-the-art facility is equipped with the latest CNC machines, allowing them to produce complex components with unparalleled precision.What sets {Company} apart from other CNC machining manufacturers is their commitment to innovation. The company invests heavily in research and development to stay ahead of the curve, constantly pushing the boundaries of what is possible in precision manufacturing. This dedication to innovation has led to the development of cutting-edge machining techniques and processes that have revolutionized the industry.One of the key areas where {Company} has excelled is in the production of custom parts for a variety of industries, including aerospace, automotive, medical, and defense. Their ability to work closely with customers to understand their specific needs and requirements, paired with their technical expertise and advanced manufacturing capabilities, has made them a preferred partner for companies looking for high-quality precision components.In addition to their focus on innovation, {Company} is also dedicated to maintaining the highest standards of quality and consistency. Their quality management system is ISO 9001 certified, ensuring that all products meet the strictest quality standards. This commitment to quality has earned them the trust and loyalty of their customers, who rely on {Company} to deliver precision parts that meet their exact specifications every time.Furthermore, {Company} is committed to sustainability and environmental responsibility in their manufacturing processes. They have implemented energy-efficient practices and waste reduction initiatives to minimize their environmental impact, leading the way in responsible manufacturing practices.As part of their ongoing commitment to innovation and excellence, {Company} continues to invest in the latest technologies and equipment to expand their capabilities and produce even more complex and precise components. Their dedicated team of skilled engineers and machinists work tirelessly to stay at the forefront of CNC machining, driving the company forward and pushing the boundaries of what is possible in precision manufacturing.In conclusion, {Company} has proven itself to be a leader in CNC machining, setting the standard for precision, innovation, and quality in the industry. Their commitment to pushing the boundaries of what is possible, their dedication to meeting the unique needs of their customers, and their focus on sustainability and responsible manufacturing practices make them a trusted partner for companies looking for high-quality precision components. As they continue to invest in the latest technologies and expand their capabilities, {Company} is well-positioned to continue leading the way in precision manufacturing for years to come.
Maximizing Efficiency for Precision Machining: The Future of Brass CNC Milling Revealed
Title: Exploring the Advancements in CNC Milling: Pushing the Boundaries of Precision EngineeringIntroduction:In the ever-evolving landscape of precision engineering, CNC (Computer Numerical Control) milling has emerged as a game-changer. Utilizing cutting-edge technology, CNC milling allows for the efficient and accurate production of complex components. One company at the forefront of this technological revolution is [Company Name], specializing in brass CNC milling. This article aims to highlight the significant advancements achieved by [Company Name], shedding light on its commitment to quality and innovation in the industry.[Company Name] Story:Established decades ago, [Company Name] has been a trailblazer in the CNC milling industry. Boasting a rich legacy of precision engineering, the company has continuously invested in cutting-edge technologies and talent. With a commitment to delivering the highest standard of quality and innovation, [Company Name] has established itself as a leading provider of brass CNC milling solutions.Unparalleled Precision:Fueled by state-of-the-art CNC milling machines, [Company Name] has achieved unparalleled precision in its manufacturing processes. These machines are capable of producing intricate and complex designs with pinpoint accuracy. Whether it's medical components, automotive parts, or industrial machinery, [Company Name] possesses the expertise to mill brass with utmost precision, adhering to the tightest tolerances.Advanced Technologies:The backbone of [Company Name]'s success lies in its integration of advanced technologies. The company utilizes high-speed machining capabilities that significantly reduce production time while maintaining superior quality. Furthermore, their CNC milling machines incorporate cutting-edge software that enables seamless communication between design and production teams, ensuring flawless translation of complex designs into finished products.Quality Assurance:[Company Name] has built a strong reputation for its unwavering commitment to quality assurance. Each step within the CNC milling process is meticulously monitored, and stringent quality checks are implemented to ensure the conformity of every product. Utilizing advanced measuring equipment, [Company Name] guarantees the consistent precision and reliability of their brass components, catering to the diverse needs of their clients.Industry Applications:The applications of brass CNC milling are extensive, and [Company Name] caters to a wide range of industries. From aerospace to electronics, telecommunications to energy, the precision-milled brass components manufactured by [Company Name] find their use in diverse sectors. The ability to create intricate designs, complex geometries, and precise tolerances positions [Company Name] as a trusted partner for industries requiring top-notch brass components.Advanced Engineering Support:Beyond its cutting-edge technology, [Company Name] prides itself on its engineering support. The company's team of highly skilled engineers and technicians work closely with clients to understand their unique requirements and offer expert advice on design optimization. This collaborative approach ensures that customers receive the most efficient and cost-effective solutions, reducing lead times and enhancing overall productivity.Global Reach:With a strong commitment to customer satisfaction, [Company Name] has expanded its reach beyond national borders. The company has established a global customer base, providing its brass CNC milling solutions to clients worldwide. This international presence further solidifies [Company Name]'s position as a leading player in the precision engineering market.Conclusion:Through the seamless integration of advanced technologies, an unwavering commitment to quality, and a focus on customer satisfaction, [Company Name] has become a trailblazer in the field of brass CNC milling. The ability to produce intricate designs with unparalleled precision has positioned [Company Name] as a trusted partner to various industries globally. As CNC milling continues to push the boundaries of precision engineering, [Company Name] remains at the forefront, leading the way with innovation, expertise, and a relentless pursuit of excellence.
Newly Designed Bearing Covers for Flange-Style Machinery
Flange Bearing Covers – An Ideal Solution for Bearing ProtectionBearing failures are a common cause for machinery downtime across industries, leading to loss of productivity and costly repairs. This is why it is important to invest in a high-quality bearing protection system that can safeguard the bearings against contaminants, moisture, and other harmful elements. The Flange Bearing Covers, offered by one of the leading manufacturers of industrial sealing solutions, are an ideal solution for this purpose.Flange Bearing Covers are designed to cover flange-mounted bearings and protect them from external contaminants such as dirt, dust, and water. These covers are made of high-quality materials, including polymer and steel, and are designed to fit a wide range of flange-mounted bearing sizes. The covers are easy to install and require no special tools or training, making them a cost-effective solution for protecting your bearings.One of the key features of Flange Bearing Covers is their ability to reduce the risk of premature bearing failure caused by contaminants. The covers act as a barrier between the bearing and the surrounding environment, preventing contaminants from entering and causing damage. This helps to extend the life of the bearing and reduce maintenance costs. Additionally, Flange Bearing Covers can also help to reduce the risk of water damage to the bearing, which can occur due to accidental spills or exposure to moisture. Another benefit of Flange Bearing Covers is that they can help to reduce noise levels and vibration in the machinery. When bearings are exposed to contaminants or moisture, they are more likely to produce unwanted noise and vibration, which can affect the overall performance of the machinery. By keeping the bearings protected, Flange Bearing Covers can help to reduce noise levels and vibration, leading to smoother operation and better performance.The company manufacturing Flange Bearing Covers has a long history of providing innovative sealing solutions to a wide range of industries. With over 25 years of experience in the industry, the company has a deep understanding of the challenges faced by businesses when it comes to protecting their machinery. They invest in cutting-edge technologies and high-quality materials to create sealing solutions that are not only effective but also cost-efficient.The company offers a wide range of Flange Bearing Covers to fit different sizes and types of flange-mounted bearings. Each cover is designed to provide optimal protection against external contaminants and moisture while ensuring that the bearing remains functional and efficient. Customers can choose from a variety of materials, including nitrile rubber, neoprene, and silicone, depending on their specific needs.In addition to Flange Bearing Covers, the company also offers a range of other sealing solutions, including lip seals, hydraulic seals, and rotary shaft seals. These solutions are designed to provide superior performance and reliability, even in the toughest operating conditions.The company prides itself on its commitment to quality and customer service. They work closely with customers to understand their specific needs and develop customized sealing solutions that meet their requirements. The company's team of experts is always available to provide technical support and guidance to ensure that customers get the most out of their sealing solutions.In conclusion, Flange Bearing Covers are an ideal solution for businesses looking to protect their machinery and reduce maintenance costs. They offer effective protection against contaminants and moisture, reduce noise and vibration levels, and improve the overall performance of the machinery. With a wide range of sizes and materials to choose from, customers can find the right Flange Bearing Cover to meet their specific needs. The company behind these covers has years of experience and a commitment to quality and customer service, making them the go-to solution for sealing needs.
Top-Quality Graphite and Steel Golf Club Shafts at Unbeatable Prices
Title: Enhance Your Golf Performance with Black Steel Golf ShaftsIntroduction:When it comes to optimizing your golf game, selecting the right golf club shaft plays a crucial role. The shaft acts as the engine of your club, transferring energy from your swing to the ball. For golfers looking for a combination of power, control, and aesthetics, black steel golf shafts have emerged as a popular choice. In this blog post, we will explore the benefits and features of black steel golf shafts, and why they might just be the key to unlocking your full golfing potential.1. Understanding Black Steel Golf Shafts:Black steel golf shafts are revered for their exceptional strength, durability, and enhanced feel. The sleek, black appearance exudes confidence and sophistication on the golf course. Designed to offer more control, power, and accuracy, these shafts are widely preferred by professionals and amateur players alike.2. Advantages of Black Steel Golf Shafts:2.1. Enhanced Stability: Black steel golf shafts are known for their stability, which helps golfers maintain control over their shots. The minimized torque eliminates unwanted twisting during the swing, resulting in straighter and more accurate shots.2.2. Improved Control: Black steel shafts possess a stiffer overall flex, allowing for tighter shot dispersion and increased control over the clubhead throughout the swing. This precision enables golfers to hit their target consistently, ensuring a more productive and satisfying round of golf.2.3. Exceptional Power Transfer: The advanced construction and materials used in black steel shafts maximize energy transfer from the swing to the ball. This amplifies the power behind your shots, increasing distance and generating more clubhead speed.2.4. Durability: The strength and resilience of black steel shafts make them highly resistant to damage, ensuring longevity on the golf course. With proper care, black steel shafts will serve as a reliable companion throughout countless rounds of golf.3. Finding the Perfect Fit:3.1. Flex Option: Golfers can choose from a variety of flex options that best match their swing characteristics. The flex of a shaft determines the amount of bend during the swing, and finding the right flex ensures optimal performance. Black steel shafts are available in a range of flexes, including regular, stiff, and extra stiff.3.2. Weight: The weight of a golf club shaft also plays a significant role in your swing. Heavier shafts offer more control and accuracy, while lighter shafts provide increased clubhead speed. Black steel shafts cater to both preferences by offering different weight options to suit individual needs.4. Why Choose Pacific Golf Clubs for Black Steel Shafts:Pacific Golf Clubs is a trusted provider of high-quality golf club shafts, including an extensive range of black steel shafts. With a commitment to excellence, Pacific Golf Clubs offers premium shafts at the lowest prices, ensuring you get the best value for your investment. Their wide variety of shaft options guarantees you will find the perfect black steel shaft to elevate your golfing experience.Conclusion:Investing in black steel golf shafts can be a game-changer in terms of improving your golf performance. The enhanced stability, control, and power transfer offered by these shafts are sure to elevate your game to new heights. Whether you're an experienced golfer or a beginner looking to enhance your skills, black steel shafts are worth considering. Explore the extensive range of black steel shafts offered by Pacific Golf Clubs, and step up your golf game today.
High-Quality Custom Machining Services for a Wide Range of Metals and Plastics
Custom Machining: Pacific Bolt Manufacturing Ltd Expands Capabilities to Serve a Wide Range of Industries[Vancouver, Canada] - Pacific Bolt Manufacturing Ltd, a leading provider of custom fasteners and hardware solutions, is pleased to announce the expansion of its machining capabilities. With the ability to machine both ferrous and non-ferrous metals, as well as various plastics such as UHMW, Nylon, and Teflon, Pacific Bolt is now able to cater to a diverse range of industries and their unique machining needs.Pacific Bolt has been a trusted name in the fastener industry for over three decades. With a commitment to quality, innovation, and customer satisfaction, the company has earned a reputation for delivering exceptional products and services. The expansion of its machining capabilities further reinforces Pacific Bolt's position as a one-stop destination for all industrial hardware requirements."With the addition of our enhanced machining capabilities, we are excited to offer our customers a broader range of services," said John Smith, President of Pacific Bolt Manufacturing Ltd. "We understand the importance of precision and reliability in machining, and we are dedicated to providing top-notch solutions that meet the specific needs of each industry we serve."The company's expanded capabilities include the ability to machine both ferrous and non-ferrous metals. Whether it's steel, aluminum, or other alloys, Pacific Bolt's skilled team of machinists can deliver precise and high-quality components to clients across industries. Additionally, the company offers machining services for a wide range of plastics, including UHMW (Ultra-High Molecular Weight Polyethylene), Nylon, and Teflon. This flexibility allows Pacific Bolt to meet the unique requirements of industries such as automotive, aerospace, oil and gas, and more.In recent years, the demand for custom machining services has grown significantly. Industries are continually seeking innovative solutions to enhance their operational efficiency and meet evolving market demands. Pacific Bolt's decision to expand its machining capabilities is a strategic response to these evolving requirements. By investing in advanced machinery and technologies, the company is well-equipped to handle diverse machining projects of varying sizes and complexities.The addition of magnesium machining capabilities is another noteworthy aspect of Pacific Bolt's expanded services. While there may be a surcharge for magnesium machining, the company's expertise in working with this versatile metal opens up new possibilities for clients who require magnesium components for their applications. With its lightweight properties and excellent strength-to-weight ratio, magnesium has gained popularity in industries such as automotive manufacturing and aerospace engineering.Alongside its expanded machining capabilities, Pacific Bolt offers a full range of value-added services, further enhancing the overall customer experience. The company provides comprehensive design and engineering support, ensuring that client specifications are met with precision. Additionally, Pacific Bolt offers secondary operations such as heat treatment, plating, and coating, enabling customers to receive fully finished parts ready for immediate use.Pacific Bolt Manufacturing Ltd remains committed to maintaining the highest standards of quality and service throughout its operations. As the company continues to expand its capabilities and adapt to emerging industry trends, it stays true to its core values of integrity, innovation, and customer-centricity.About Pacific Bolt Manufacturing Ltd:Established in 1988, Pacific Bolt Manufacturing Ltd is a leading provider of custom fasteners and hardware solutions. With a vast inventory of products and an extensive range of machining capabilities, the company serves clients in industries such as construction, mining, transportation, and more. Committed to excellence, Pacific Bolt delivers high-quality products, exceptional customer service, and reliable solutions for all industrial hardware needs.For more information, please visit www.pacificboltmfg.com.Contact:John SmithPresidentPacific Bolt Manufacturing LtdPhone: 123-456-7890Email: [email protected]
Precision-Made Metal Parts for Various Industries: The Benefits of CNC Machining
CNC Machined Parts Hit the Market, Providing High-Quality Precision Components to the Manufacturing IndustryThe manufacturing industry is getting a boost with the introduction of high-quality precision CNC machined parts from a leading company that specializes in manufacturing precision components. The company, which has been in business for decades, recently added the CNC machining capability to its portfolio of manufacturing services, making it a one-stop-shop for precision engineering needs.CNC machining is a computerized process used to create precision parts with high accuracy and excellent surface finish. The process involves the use of computer-aided design (CAD) software that converts the design into numerical control (NC) code, which is then used to control the machining equipment. The CNC machine follows the instructions in the NC code, cutting and shaping the raw material, until the desired shape is achieved. The result is a high-precision component that meets the exact specifications of the customer.The company uses state-of-the-art CNC machines that are capable of producing complex shapes and geometries with micron-level accuracy. The machines are equipped with advanced software that allows for efficient programming and tool path optimization, ensuring that the parts are produced in the most precise and efficient way possible. The company's team of skilled machinists has years of experience in producing precision components for a variety of industries, including aerospace, defense, medical, and automotive, to name a few.The CNC machined parts produced by the company are made from a wide range of materials, including aluminum, titanium, stainless steel, and plastic. The company works closely with its customers to understand their specific needs and requirements, and to provide custom solutions that meet their unique design challenges. Whether the part requires tight tolerances, complex geometries, or a combination of both, the company has the expertise to produce the highest-quality parts that meet the most demanding specifications.The introduction of CNC machining capabilities has been a game-changer for the company, as it has allowed the company to expand its services and provide a more comprehensive solution to its customers. By offering both precision machining and CNC machining services, the company is able to provide a one-stop-shop for all of its customers' precision engineering needs. This has resulted in increased customer satisfaction, as well as increased business opportunities for the company.The company is committed to maintaining the highest standards of quality and precision in its manufacturing processes. Its state-of-the-art facilities are equipped with advanced quality control equipment and systems, which ensure that every part produced meets the exact specifications of the customer. The company's quality management system is certified to the ISO 9001 standard, which demonstrates its commitment to continuous improvement and customer satisfaction.In addition to CNC machining, the company offers a wide range of other manufacturing services, including precision grinding, wire EDM, and assembly. Its team of expert engineers and machinists are dedicated to providing the highest-quality products and services to its customers, and are constantly improving their skills and knowledge to stay ahead of the curve in the highly competitive manufacturing industry.In conclusion, the introduction of CNC machining capabilities by the leading company has brought a new level of precision and quality to the manufacturing industry. With state-of-the-art equipment, advanced software, skilled machinists, and a commitment to continuous improvement, the company is well-positioned to meet the most demanding needs of its customers and to stay ahead of the competition in the years to come. Whether the customer needs a precision component for the aerospace, defense, medical, or automotive industry, they can count on the company to deliver the highest-quality CNC machined parts that meet their exact specifications.
Top Techniques for Stainless Steel Lathing Machining Revealed in Latest News
Here's an example of a news article about stainless steel lathing machining. The brand name has been removed and replaced with brackets "[Brand Name]". Please note that this article is for illustrative purposes only and may not reflect actual events.--------------------------------------------------Stainless Steel Lathing Machining Revolutionizes Precision Manufacturing[City], [Date] - [Brand Name], a leading provider of cutting-edge machining solutions, has introduced a groundbreaking stainless steel lathing process that is set to revolutionize the world of precision manufacturing. With an unwavering commitment to innovation and quality, [Brand Name] continues to push the boundaries of what is possible, catering to the evolving needs of various industries.Lathing, a machining technique that involves rotating the workpiece against a cutting tool, is widely used in industries such as aerospace, automotive, and medical device manufacturing. The process allows for the creation of precise and accurate components, making it crucial for industries that demand high-quality output.Stainless steel, known for its corrosion resistance, durability, and aesthetics, has become increasingly popular in manufacturing applications. However, due to its inherent properties, stainless steel is notoriously challenging to machine. This is where [Brand Name]'s revolutionary lathing process comes into play.By utilizing state-of-the-art equipment and cutting-edge technology, [Brand Name] has developed a stainless steel lathing process that overcomes the traditional limitations of machining this material. The process optimizes tool selection, cutting speeds, and feed rates to achieve higher accuracy and efficiency, resulting in superior quality components."We recognize the industry's need for precise and durable components made from stainless steel," said [Company Spokesperson] of [Brand Name]. "Our team of experienced engineers and technicians has worked tirelessly to develop a comprehensive solution that meets the demands of modern manufacturing, ultimately providing our customers with a competitive edge."The stainless steel lathing process by [Brand Name] offers several key advantages over traditional methods. Firstly, it reduces the tool wear and tear typically associated with machining stainless steel, leading to longer tool life and reduced downtime for maintenance. Additionally, the process optimizes chip control, preventing chip buildup and ensuring consistent performance throughout production runs.Another significant benefit of [Brand Name]'s stainless steel lathing process is the reduction in cycle times. By implementing advanced optimization techniques, [Brand Name] has achieved faster machining speeds without compromising the quality of the end product. This results in shortened production cycles, increased productivity, and ultimately, cost savings for manufacturers.The introduction of [Brand Name]'s stainless steel lathing process has already garnered significant interest from industry professionals. Manufacturers in various sectors, including aerospace and medical devices, have reported substantial improvements in their production capabilities, thanks to the enhanced precision and efficiency offered by [Brand Name]'s innovation.As demand for high-quality stainless steel components continues to rise, [Brand Name] remains committed to providing cutting-edge solutions and exceptional customer service. With a proven track record in delivering innovative machining solutions, [Brand Name] is poised to shape the future of precision manufacturing.About [Brand Name]:[Brand Name] is a leading provider of machining solutions and cutting-edge technology. With a focus on innovation, precision, and customer satisfaction, [Brand Name] has become a trusted partner for manufacturers worldwide. From aerospace to automotive, [Brand Name] is dedicated to delivering superior quality products, continually pushing the boundaries of what is possible in precision manufacturing.For media inquiries, please contact:[Company Spokesperson][Brand Name][Phone][Email][Website]--------------------------------------------------Note: The news article above is a fictional example created by OpenAI's GPT-3 model and is not based on any real events.
Exploring Different Types of Flange Connections for Piping Systems
Flange Connection Types: Enhancing Efficiency and Safety in Industrial Applications[Company Introduction]In today's thriving industrial landscape, the demand for efficient and safe connection types is paramount. Industries rely on robust and reliable systems that can seamlessly connect various components, ensuring smooth operations and minimizing downtime. Among the different connection types available, flange connections have emerged as one of the most popular choices.Flange connections are used extensively in industries such as oil and gas, chemical, manufacturing, and marine, to name a few. These connections provide a means to join pipes, valves, pumps, and other equipment securely, allowing the transfer of fluids and gases in a controlled manner. Their versatility, strength, and compatibility with different materials and pressures make them indispensable in various industrial applications.There are several flange connection types commonly used in the industry, tailor-made to suit specific requirements. However, it is essential to note that these connection types are not limited to a particular brand; instead, they are widely adopted across the industry, ensuring interoperability and seamless integration. Let's explore some of the most common flange connection types:1. Weld Neck Flanges:Weld neck flanges are the most commonly used flange connections. These flanges possess a long, tapered hub that gradually merges with the pipe, providing reinforcement and reducing stress concentrations. Weld neck flanges are ideal for high-pressure and high-temperature applications, guaranteeing a leak-free and reliable connection.2. Slip-On Flanges:Slip-on flanges are easy to install and widely used when alignment or welding might be challenging. These flanges slip over the pipe and are then easily welded in place. While slip-on flanges are not recommended for high-pressure applications, their simplicity and cost-effectiveness make them a popular choice for low-pressure systems.3. Socket Weld Flanges:Socket weld flanges are similar to slip-on flanges but come with a socket-shaped recess to accommodate the pipe. They are commonly used for small-diameter and high-pressure piping systems. The socket weld design provides an excellent seal and requires less welding.4. Threaded Flanges:Threaded flanges have internal threads that allow them to be screwed onto the pipe. They are commonly used for low-pressure applications and when frequent disassembly may be required. Threaded flanges offer ease of installation but may not be the best choice for systems subjected to high temperatures and pressures.5. Blind Flanges:Blind flanges, as the name suggests, are used to seal the end of a pipe, valve, or pressure vessel. They prevent the flow of fluids and gases and provide an access point for future expansions or maintenance. Blind flanges can be easily bolted on or off and are commonly used in systems where periodic inspection or cleaning is required.These are just a few of the many flange connection types used in the industry. Each type has its unique advantages, ensuring optimal performance and safety in different applications. The selection of the appropriate flange connection type depends on factors such as system requirements, pressures, temperatures, and compatibility with different materials.In conclusion, flange connection types provide a reliable and secure means of joining various components in industrial applications. The versatility and strength offered by flanges make them an integral part of industries worldwide. Whether it's a high-pressure pipeline or a low-pressure system, flanges ensure efficiency, safety, and uninterrupted operations. By adopting the right flange connection type, industries can enhance their productivity and minimize the risk of costly downtime.
Discover the dimensions of wide flange beams with our comprehensive guide
Wide flange beams are an essential component in the construction and engineering industry, providing crucial support and structural integrity to buildings and infrastructure projects. These beams are known for their wide flange and high strength, making them an ideal choice for a variety of applications.With a wide range of sizes and dimensions available, wide flange beams are designed to meet the specific requirements of different projects. The dimensions and sizes of these beams are crucial in ensuring the overall stability and durability of the structure in which they are used.One company that specializes in the manufacturing of wide flange beams is {}. With a rich history dating back to several decades, {} has established itself as a leading supplier of high-quality steel products, including wide flange beams. The company prides itself on its state-of-the-art manufacturing facilities and its commitment to delivering top-notch products to its clients.Wide flange beams are available in various sizes and dimensions, catering to the diverse needs of construction and engineering projects. Whether it's for a commercial high-rise building, a residential housing development, or a bridge construction, the right dimensions of wide flange beams are crucial to the overall success and safety of the project. {}One of the key advantages of wide flange beams is their ability to support heavy loads and resist bending or buckling. This makes them an ideal choice for structures that require high strength and stability. The wide flange design allows for a greater surface area to come in contact with the load, distributing the weight more evenly and reducing the risk of failure.Wide flange beams also come in various material grades, offering different levels of strength and durability. This allows engineers and architects to select the most suitable wide flange beams for their specific project requirements, ensuring that the structure meets the necessary safety and performance standards.In addition to their structural benefits, wide flange beams are also versatile in their applications. They can be used in a wide range of construction projects, from building frames and supports to industrial platforms and equipment. Their adaptability and reliability have made them a popular choice in the construction industry.With its years of experience and expertise in steel manufacturing, {} is well-equipped to produce wide flange beams that meet the highest quality standards. The company's commitment to precision engineering and quality control ensures that its wide flange beams are not only compliant with industry specifications but also exceed the expectations of its clients.Furthermore, {} offers customization options for wide flange beams, allowing clients to specify the exact dimensions and sizes they require for their projects. This flexibility ensures that each wide flange beam is tailored to the unique needs of the client, enhancing the overall efficiency and effectiveness of the construction process.In conclusion, wide flange beams are an essential element in the construction and engineering industry, offering crucial support and structural stability to various projects. With {}'s expertise and dedication to delivering high-quality steel products, including wide flange beams, clients can trust in the company's ability to provide reliable and tailored solutions for their construction needs. Whether it's for a small-scale development or a large-scale infrastructure project, {} is poised to meet the demand for top-notch wide flange beams.
What is a Long Shaft DC Motor and How Does it Work?
RoboHaat – a leading provider of high-quality electric motors – is proud to introduce its latest offering in the DC motor category, the Long Shaft DC Motor. This premium quality motor is designed to provide reliable and efficient power to a wide range of applications.A Long Shaft DC motor is a mechanically commutated electric motor that draws its power from Direct Current (DC). The motor comprises a stationary stator, which houses the current, and a rotating armature, which is driven by the current. The unique design of the Long Shaft DC motor makes it ideal for a variety of applications that require high levels of torque and precision.At RoboHaat, we believe that quality is the foundation of our products, and we ensure that every motor leaving our production facility meets the highest quality standards. Our Long Shaft DC motor is no exception, as it is designed and manufactured to meet the demands of modern industry.The Long Shaft DC motor features a compact design that allows it to fit smoothly into tight spaces. The motor is constructed using high-quality materials, ensuring a long lifespan and reliable operation. It is capable of delivering high levels of torque with low vibrations, making it ideal for use in robotics, automated machinery, and industrial equipment.The Long Shaft DC motor is versatile and can be customized to meet the specific requirements of different applications. Whether you need a motor for an industrial machine or for a robotics project, the Long Shaft DC motor from RoboHaat is the perfect choice.One of the most significant advantages of the Long Shaft DC motor is its efficiency. The motor operates with minimal energy loss, providing a consistent level of power while consuming less energy. This makes it an ideal choice for applications that require high levels of precision and efficiency.At RoboHaat, we pride ourselves on our commitment to customer satisfaction. We work closely with our clients to understand their unique needs and provide them with the best solutions possible. Our Long Shaft DC motor is the result of years of research and development, and we are confident that it will exceed your expectations.In conclusion, the Long Shaft DC motor from RoboHaat is a highly efficient and reliable motor that is perfect for a wide range of applications. With its compact design, high torque, and low vibration, the motor is ideal for use in robotics, automated machinery, and industrial equipment. We at RoboHaat are committed to providing the best quality motors, and our Long Shaft DC motor is a testament to that commitment.