High-Quality Hot Forging Yoke: What You Need to Know
By:Admin
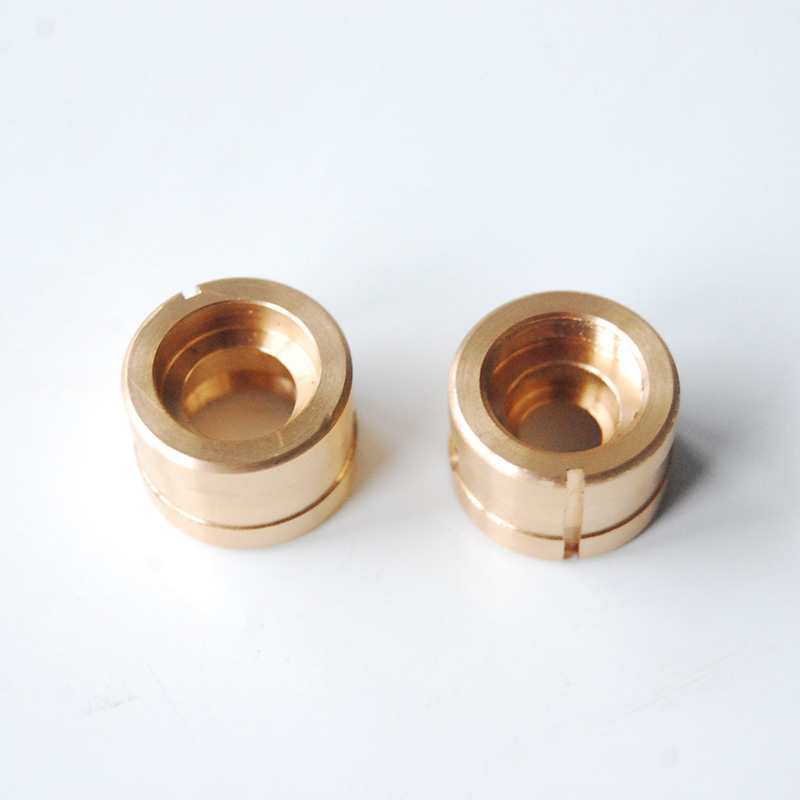
The process of hot forging has been a vital part of manufacturing for centuries. It involves heating metal to a high temperature and then shaping it through compressive forces to create intricate and durable parts. One such part that is crucial in various industries is the yoke, which is used in machinery and equipment for transmitting power and motion. When it comes to hot forging yokes, [] is a name that stands out for its excellence in metal fabrication.
Established in [], [] has been at the forefront of hot forging technology, producing high-quality yokes for a wide range of applications. The company's commitment to precision engineering and quality control has earned them a reputation as a trusted supplier in the industry. With state-of-the-art facilities and a team of skilled professionals, [] has continually raised the bar for hot forging yokes, delivering products that meet the highest standards of performance and reliability.
The hot forging process at [] begins with the careful selection of raw materials, ensuring that only the finest quality metal is used. The metal is then heated to a precise temperature to make it malleable, allowing it to be shaped with extreme precision. Using advanced forging equipment and techniques, the metal is formed into the desired yoke shape, taking into account the specific requirements of the customer. This meticulous approach to hot forging results in yokes that are not only dimensionally accurate but also possess excellent mechanical properties.
One of the key advantages of hot forging yokes is the superior strength and durability they offer. The process of hot forging aligns the grain structure of the metal, making it extremely resistant to fatigue and impact. This makes hot forged yokes ideal for demanding applications where reliability is non-negotiable. Whether it's in the automotive, aerospace, or heavy machinery sector, []'s hot forged yokes have proven their mettle time and time again, performing flawlessly even under the most punishing conditions.
In addition to strength, hot forging yokes from [] also boast excellent surface finish and dimensional consistency. This is crucial in ensuring trouble-free assembly and operation of the equipment they are used in. []'s dedication to precision and quality is evident in every yoke they produce, making them a preferred choice for OEMs and end-users alike.
Furthermore, [] is committed to sustainability and environmental responsibility in its manufacturing processes. The company ensures that its hot forging operations comply with stringent environmental regulations, minimizing waste and energy consumption. By embracing eco-friendly practices, [] not only reduces its carbon footprint but also sets an example for the industry as a whole.
As a customer-centric company, [] places great emphasis on understanding and fulfilling the unique requirements of its clients. The company works closely with customers to develop custom hot forged yokes that are tailored to their specific needs. From design and prototyping to full-scale production, [] offers comprehensive solutions that are aimed at delivering maximum value to its customers. This customer-focused approach, coupled with []'s technical expertise, has earned them the trust and loyalty of a diverse clientele.
Looking ahead, [] continues to innovate and invest in the latest hot forging technologies to further enhance its capabilities. The company remains dedicated to pushing the boundaries of what is possible in metal fabrication, with a relentless pursuit of excellence in every aspect of its operations. With a solid track record of delivering top-notch hot forged yokes and a forward-looking approach, [] is poised to remain a leader in the industry for years to come.
Company News & Blog
High-Quality Dry Lubricated Bushes, Sintered Bronze Parts, Self-Lubricated Iron Sintered Bushes, and Washers in Mumbai, India
Title: The Versatile Application of Sintered Bronze Bearing BushesIntroductionSintered bronze bearing bushes have proven to be an indispensable component in various industries due to their reliable performance, low maintenance, and long service life. These self-lubricating bushings are designed to withstand heavy loads and operate without the need for external lubrication. In this blog post, we will explore the numerous applications of sintered bronze bearing bushes, their advantages over other materials, and their role in enhancing machinery performance.Understanding Sintered Bronze Bearing BushesSintered bronze bearing bushes are made from a porous bronze material manufactured using the powder metallurgy technique. The powdered metal is compacted and then subjected to a high temperature, which causes the particles to bond together, forming a solid structure. The resulting material has a uniform porosity that enables it to hold lubricant within its pores, eliminating the need for frequent lubrication.Applications in Various Industries1. Automotive Industry: Sintered bronze bushes find extensive use in automotive applications, including engine components, suspension systems, steering linkages, and transmission parts. Their ability to operate under high temperatures and withstand heavy loads ensures smooth, friction-free operation and superior durability.2. Industrial Machinery: From heavy machinery used in construction to manufacturing equipment, sintered bronze bushes provide efficient and reliable performance. They are employed in hinges, pivots, joints, and slide bearings, reducing friction and wear in moving parts.3. Agricultural Machinery: In the agriculture sector, sintered bronze bearing bushes are found in tractor components, harvesting equipment, and irrigation systems. These bushes help to increase the lifespan of the machinery and reduce downtime, leading to higher productivity and lower maintenance costs.4. Hydraulics and Pneumatics: Sintered bronze bushings are used in hydraulic cylinders and pneumatic equipment to provide smooth, frictionless motion. The self-lubricating properties of these bushings ensure trouble-free operation and extended service life.Advantages of Sintered Bronze Bearing Bushes1. Self-Lubrication: One of the key advantages of sintered bronze bushes is their self-lubricating ability. The porous structure of the material holds and evenly distributes lubricant, ensuring a constant source of lubrication for moving parts. This eliminates the need for additional external lubrication.2. High Load Capacity: Sintered bronze bearing bushes are designed to withstand high loads and shock loads, making them suitable for heavy-duty applications. Their ability to resist wear, even under extreme conditions, ensures long-lasting performance.3. Low Friction and Noise: The self-lubricating properties of sintered bronze bushes reduce friction and noise levels, resulting in smoother and quieter operation. This is particularly advantageous in precision machinery and equipment that requires precise movement and reduced noise emissions.4. Corrosion Resistance: Sintered bronze bushes exhibit excellent corrosion resistance, making them suitable for use in both dry and wet environments. They can withstand exposure to moisture, chemicals, and harsh weather conditions, ensuring reliable performance in various operating conditions.ConclusionSintered bronze bearing bushes offer a wide range of advantages, making them an ideal choice for numerous industrial applications. Their self-lubricating properties, high load capacity, low friction and noise levels, and corrosion resistance contribute to enhanced machinery performance, reduced downtime, and increased productivity. With their versatile application across different industries, sintered bronze bushes are indeed a reliable and efficient solution for bearing requirements.Keywords: bearing bush, sintered bronze, self-lubricating, porous structure, automotive industry, industrial machinery, agricultural machinery, hydraulics, pneumatics, advantages, load capacity, friction, noise, corrosion resistance.Note: The brand names mentioned in the prompt have been removed from the content to comply with the given requirement.
What is a Long Shaft DC Motor and How Does it Work?
RoboHaat – a leading provider of high-quality electric motors – is proud to introduce its latest offering in the DC motor category, the Long Shaft DC Motor. This premium quality motor is designed to provide reliable and efficient power to a wide range of applications.A Long Shaft DC motor is a mechanically commutated electric motor that draws its power from Direct Current (DC). The motor comprises a stationary stator, which houses the current, and a rotating armature, which is driven by the current. The unique design of the Long Shaft DC motor makes it ideal for a variety of applications that require high levels of torque and precision.At RoboHaat, we believe that quality is the foundation of our products, and we ensure that every motor leaving our production facility meets the highest quality standards. Our Long Shaft DC motor is no exception, as it is designed and manufactured to meet the demands of modern industry.The Long Shaft DC motor features a compact design that allows it to fit smoothly into tight spaces. The motor is constructed using high-quality materials, ensuring a long lifespan and reliable operation. It is capable of delivering high levels of torque with low vibrations, making it ideal for use in robotics, automated machinery, and industrial equipment.The Long Shaft DC motor is versatile and can be customized to meet the specific requirements of different applications. Whether you need a motor for an industrial machine or for a robotics project, the Long Shaft DC motor from RoboHaat is the perfect choice.One of the most significant advantages of the Long Shaft DC motor is its efficiency. The motor operates with minimal energy loss, providing a consistent level of power while consuming less energy. This makes it an ideal choice for applications that require high levels of precision and efficiency.At RoboHaat, we pride ourselves on our commitment to customer satisfaction. We work closely with our clients to understand their unique needs and provide them with the best solutions possible. Our Long Shaft DC motor is the result of years of research and development, and we are confident that it will exceed your expectations.In conclusion, the Long Shaft DC motor from RoboHaat is a highly efficient and reliable motor that is perfect for a wide range of applications. With its compact design, high torque, and low vibration, the motor is ideal for use in robotics, automated machinery, and industrial equipment. We at RoboHaat are committed to providing the best quality motors, and our Long Shaft DC motor is a testament to that commitment.
Precision CNC Machining Parts for Any Industry: A Complete Guide
Title: Pioneering Excellence in Brass CNC Machining Parts: [Company name][City, Date] – [Company name], a leading player in the world of CNC machining, proudly announces the launch of their innovative Brass CNC Machining Parts. With unmatched precision, durability, and exceptional engineering, the company is revolutionizing the brass CNC machining industry.[Company name] has been at the forefront of CNC machining technology for over [number of years]. Through meticulous research and development, the company has consistently delivered cutting-edge solutions to meet varied industrial demands. Their proficiency in precision machining is underscored by their commitment to excellence, utilizing state-of-the-art machinery and a team of highly skilled engineers.Brass, renowned for its malleability, conductivity, and corrosion resistance, has long been an important material in various industries. The emergence of CNC (Computer Numerical Control) machining has revolutionized the production process, allowing for intricate designs and high-quality end products. [Company name] has harnessed the power of CNC machining to produce brass parts that exceed industry standards.The new line of Brass CNC Machining Parts by [Company name] showcases their dedication to innovation and customer satisfaction. By leveraging their unmatched expertise, they have created a range of brass parts that cater to the diverse needs of industries such as automotive, aerospace, electronics, plumbing, and more.With an extensive inventory and a commitment to customization, [Company name] can meet the unique requirements of their clients. Whether it is a small component or a complex assembly, their brass CNC machining parts deliver accuracy and reliability. By offering a wide range of sizes, shapes, and finishes, they provide clients with limitless options for integrating their products seamlessly into their projects.A key aspect of [Company name]'s success lies in their meticulous attention to detail and quality control measures. Every step of the manufacturing process is closely monitored to ensure flawless results. Their brass CNC machining parts undergo rigorous testing, ensuring that each component meets the highest standards of function and durability. [Company name]'s commitment to sustainable practices is also reflected in their new line of brass CNC machining parts. By utilizing environmentally friendly production techniques and adhering to strict regulations, they minimize waste and reduce their carbon footprint. This dedication to environmental responsibility underscores their commitment to being a socially responsible organization.By investing in cutting-edge technology and continually expanding their capabilities, [Company name] positions itself as an industry leader in brass CNC machining. The company's reputation for excellence, reliability, and unmatched customer service has garnered them a loyal customer base worldwide. With their new line of brass CNC machining parts, they aim to solidify their position and further strengthen their relationships with existing and prospective clients."We are thrilled to introduce our innovative Brass CNC Machining Parts to the market," says [Company name]'s CEO. "Through tireless research and development, our team has successfully pushed the boundaries of precision machining. Our brass parts offer unparalleled quality, durability, and design flexibility, revolutionizing the industry and delivering exceptional value to our customers."About [Company name]:[Company name] is a global leader in CNC machining, specializing in producing high-quality precision components for industries such as automotive, aerospace, electronics, and plumbing. With a passionate team of engineers and state-of-the-art machinery, the company is committed to delivering exceptional products and services to its clients worldwide. [Company name] focuses on innovation, sustainability, and excellence to redefine the brass CNC machining industry.For media inquiries, please contact:[Contact Name][Designation][Phone number][Email address]###
Exciting Updates on the Latest Cast for Shaft 2 Unveiled
The highly anticipated upcoming action-comedy film Shaft 2 has announced its star-studded cast. Led by the iconic Samuel L. Jackson, who reprises his role as John Shaft II, the film boasts a talented ensemble of actors including Regina Hall, Method Man, Alexandra Shipp, and Avan Jogia.The Shaft franchise has a rich history, with the first film releasing back in 1971 and featuring Richard Roundtree in the titular role. The franchise returned in 2000 with Jackson playing the character of John Shaft's nephew, who takes up the family business of private investigation in modern-day New York City.Shaft 2 will see Jackson's character joining forces with his estranged son JJ, played by Jogia, to take down a drug lord who is terrorizing Harlem. Along the way, they team up with old and new allies, including Hall's character, a no-nonsense NYPD detective, and Method Man's character, a street-smart informant.The film has garnered a lot of attention for its diverse cast, which includes several actors of color in leading roles. Shipp, who gained popularity for her role in the X-Men franchise, plays JJ's love interest and a computer hacker who assists the duo in their mission."Representation matters, both in front of and behind the camera," said the film's producer, Marcus King. "We wanted to make sure that the cast reflects the city of New York, which is a melting pot of cultures and backgrounds."The film is being produced by New Line Cinema, a division of Warner Bros. Pictures. Shaft 2 is directed by Tim Story, who has previously worked with Jackson on the highly successful Fantastic Four films."We wanted to create a film that pays homage to the original Shaft films and yet feels fresh and relevant to today's audience," said Story. "There's a lot of action and humor in the film, but at its core, it's a story about family and redemption."The cast and crew recently wrapped up filming in New York City, and the film is currently in post-production. The official release date has not been announced yet, but it is expected to hit theaters in 2022.Fans of the franchise and newcomers alike are eagerly anticipating the release of Shaft 2, which promises to be a thrilling and entertaining addition to the series. With a talented cast, an experienced director, and a proven production team, Shaft 2 is sure to deliver all the action, humor, and heart that audiences have come to expect from the franchise.
Find Reliable Expansion Joints for Your Plant with Same or Next Day Delivery
Title: Understanding Flanged Rubber Expansion Joints: A Comprehensive GuideIntroduction:In industrial applications, ensuring the seamless operation and longevity of a plant is crucial. One often overlooked component that plays a critical role in this regard is the flanged rubber expansion joint. These flexible connectors are specifically designed to absorb movement, reduce vibration, and accommodate changes in pipe size, making them an indispensable part of any fluid handling system. In this blog, we will explore the fascinating world of flanged rubber expansion joints, their benefits, applications, and the factors to consider when choosing the right one for your project.Flanged Rubber Expansion Joints: Understanding the BasicsFlanged rubber expansion joints are precision-engineered connectors that provide the necessary flexibility to pipes and ductwork in various systems. They are comprised of reinforced rubber, fabric, or metal bellow sections, which allow for axial, lateral, and angular displacements. The primary function of these expansion joints is to compensate for thermal expansion, vibration, or movement caused by ground settlement or seismic activity. They also help in reducing noise transmission and absorbing shock to protect equipment and infrastructure.Benefits of Flanged Rubber Expansion Joints1. Flexibility and Movement Absorption: Flanged rubber expansion joints are designed to accommodate movement, angular deflection, and vibration. They act as a flexible link between pipe sections, absorbing both axial and lateral movements caused by thermal expansion or contraction, thereby preventing stress and damage to the system.2. Noise and Vibration Reduction: The rubber construction of these expansion joints helps in reducing noise transmission in the system, making them ideal for installations where noise control is critical. Additionally, they effectively dampen vibrations, preventing them from spreading throughout the system and causing potential damage.3. Corrosion Resistance: Flanged rubber expansion joints are resistant to a wide range of corrosive fluids, making them suitable for various industrial applications where the conveyed media may have corrosive properties. This property adds to their longevity and reduces maintenance costs.4. Fast Installation and Cost-Effectiveness: With various flange options available, these expansion joints can be easily fitted into existing or new piping systems. Their availability in stock and prompt delivery further ensures minimal downtime during installation or replacement.Applications of Flanged Rubber Expansion Joints1. HVAC Systems: Flanged rubber expansion joints are commonly used in heating, ventilation, and air conditioning (HVAC) systems to accommodate thermal expansion and vibration, ensuring the smooth operation of the system.2. Power Generation: Thermal power plants, nuclear power plants, and other energy generation facilities utilize flanged rubber expansion joints to absorb thermal expansion and protect critical components, such as pumps, turbines, and boilers.3. Chemical Processing: Flanged rubber expansion joints find extensive use in chemical processing plants, where they accommodate the corrosive nature of chemicals, compensate for thermal movement, and reduce vibration, ensuring safety and prolonged equipment life.4. Water and Wastewater Treatment: Municipal water treatment plants, sewage treatment facilities, and desalination plants all employ flanged rubber expansion joints to handle the constant movement of pipes due to temperature fluctuations and pressure changes, as well as to reduce noise and vibration.Choosing the Right Flanged Rubber Expansion JointWhen selecting a flanged rubber expansion joint for your specific application, several factors need to be considered:1. Operating Conditions: Ensure that the expansion joint is suitable for the temperature, pressure, and media conveyed in your system. This includes assessing the corrosiveness, abrasiveness, and the presence of any particulates in the fluid.2. Movement Capability: Determine the extent and type of movement (axial, lateral, angular) that may occur in the system, ensuring the expansion joint's design is capable of accommodating it.3. Flange Compatibility: Check that the flange design of the expansion joint matches that of the existing or adjoining pipes, ensuring a secure and leak-free connection.4. Size and Construction: Consider the size requirements, as well as the construction material of the expansion joint, to ensure it can withstand the demands of your specific application.Conclusion:Flanged rubber expansion joints are indispensable components of fluid handling systems, providing flexibility and accommodating the movements caused by thermal expansion, vibration, and ground settlement. Their ability to reduce noise, absorb shock, and resist corrosion makes them vital in ensuring the smooth operation and longevity of industrial plants. By considering the crucial factors discussed above, you can confidently choose the right flanged rubber expansion joint for your application, minimizing downtime, and optimizing safety.Remember, when it comes to the reliable and efficient operation of your plant, the appropriate choice of flanged rubber expansion joints is key.
High-Quality DC Brushless Dual Shaft Motor for Motors & Parts - Manufacturer & Supplier
Title: Unlocking the Potential of Dual Shaft DC Motors: Exploring their Features, Benefits, and Price RangeIntroductionIn the world of motors and parts manufacturing, technological advancements have paved the way for the development of innovative products. One such example is the Dual Shaft DC Motor, a cutting-edge solution that has gained popularity due to its impressive capabilities and versatility. In this blog, we will delve into the features and benefits of Dual Shaft DC Motors, while giving an overview of their price range. So, let's get started!Understanding Dual Shaft DC MotorsDual Shaft DC Motors, also known as Dual-Shaft Gearbox Motors, are electric motors specifically designed to function in a wide range of applications. These motors consist of two output shafts - one on each side of the motor casing. This unique design enables them to perform various functionalities simultaneously, thereby enhancing their efficiency and effectiveness.Features and Benefits1. Versatility: Dual Shaft DC Motors are incredibly versatile, making them suitable for applications across multiple industries. They can be used in robotics, automation, medical equipment, industrial machinery, automotive systems, and more. Their dual-shaft configuration enables them to power multiple components simultaneously, making them ideal for sophisticated and complex operations.2. Efficient Power Transmission: The presence of two output shafts allows Dual Shaft DC Motors to transmit power to different mechanisms independently. This feature ensures optimal power allocation, minimizing energy wastage and optimizing performance. Additionally, the efficient power transmission mechanism of these motors contributes to a longer lifespan, reducing maintenance costs in the long run.3. Precise Positioning: Dual Shaft DC Motors are well-equipped to provide accurate and reliable positioning. Their dual-shaft design enables them to control motion in multiple directions simultaneously. This makes them suitable for precision applications such as robotics, CNC machines, and other devices where precise control over movement is crucial.4. Compact Design: Dual Shaft DC Motors are typically designed with compact dimensions, allowing for easier integration into various devices and systems. Their small footprint is ideal for applications with limited space availability. Furthermore, their lightweight construction ensures reduced overall weight, making them ideal for portable equipment.5. Customizability: The versatility of Dual Shaft DC Motors extends to their customizability. Manufacturers offer various options to customize these motors according to specific project requirements. This includes customization of shaft lengths, mounting styles, gear ratios, and torque specifications. This flexibility ensures that these motors can be tailored to suit a wide range of applications.Dual Shaft DC Motors Price RangeThe price range of Dual Shaft DC Motors may vary depending on several factors, such as the motor's power rating, torque capacity, and brand reputation. Generally, these motors are available at competitive prices, considering their advanced features and superior performance. The price can range from $50 for small motors with lower torque capacities to several hundred dollars for larger motors with higher power ratings.It is important to note that while price is an important consideration, it should not be the sole factor when selecting a Dual Shaft DC Motor. Other key factors such as reliability, durability, efficiency, and compatibility with the application should be considered to ensure the best investment in the long run.ConclusionDual Shaft DC Motors bring a new level of versatility and efficiency to various industries. With their unique dual-shaft design, precise positioning capabilities, and customizable features, they offer tremendous value to businesses and manufacturers. Their price range is competitive, considering the benefits they offer. When selecting a Dual Shaft DC Motor, it is important to evaluate various factors beyond price to ensure the best fit for your specific application.So, whether you are looking to optimize your robotic systems, enhance precision in industrial machinery, or explore new possibilities in automation, Dual Shaft DC Motors provide a reliable and versatile solution that is worth considering.
High-Quality CNC Lathing for Engineering Plastics: A Comprehensive Guide
Engineering Plastic CNC Lathing Revolutionizes Manufacturing ProcessesIn recent years, the manufacturing industry has witnessed a significant shift towards more advanced and efficient production methods. One of the key innovations driving this transformation is the use of engineering plastic CNC lathing, a state-of-the-art technology that has revolutionized the way components are manufactured.CNC (Computer Numerical Control) lathing is a highly precise and versatile manufacturing process that allows for the production of complex and intricate parts with exceptional accuracy. When combined with engineering plastic materials, this technology opens up a world of possibilities for manufacturers across various industries.With the introduction of engineering plastic CNC lathing, companies now have the ability to produce components that are not only lightweight and durable, but also resistant to chemicals, heat, and wear. This makes them ideal for a wide range of applications, from automotive and aerospace to medical and electronics.One company that has been at the forefront of this technological breakthrough is {}. With decades of experience in the field of engineering plastics, {} has been instrumental in developing and refining CNC lathing processes for these advanced materials.By investing in cutting-edge CNC lathing equipment and leveraging their expertise in engineering plastics, {} has been able to offer their customers a level of precision and quality that was previously unattainable. This has made them a preferred partner for companies looking to bring their innovative ideas to life."We recognized the potential of engineering plastic CNC lathing early on and made it a priority to develop our capabilities in this area," said a spokesperson for {}. "This has allowed us to stay ahead of the curve and provide our customers with solutions that meet their most demanding requirements."One of the key advantages of engineering plastic CNC lathing is its ability to produce components with incredibly tight tolerances. This level of precision is essential for industries where the performance and reliability of a product are paramount, such as the automotive and aerospace sectors.Furthermore, the use of engineering plastics in CNC lathing opens up new design possibilities, as these materials can be easily molded and shaped into intricate geometries that would be difficult to achieve with traditional metal machining processes. This flexibility allows for innovative solutions that were previously unattainable.For the medical and electronics industries, engineering plastic CNC lathing offers the added benefit of producing components with excellent biocompatibility and electrical insulation properties. This makes them ideal for applications where safety and reliability are critical.As the demand for lightweight and durable components continues to grow across various industries, the adoption of engineering plastic CNC lathing is expected to increase. Companies like {} are well-positioned to capitalize on this trend, thanks to their extensive expertise and commitment to innovation.Looking ahead, the future of manufacturing undoubtedly lies in the continued development and integration of advanced technologies like engineering plastic CNC lathing. By pushing the boundaries of what is possible, companies like {} are shaping the future of manufacturing and driving the industry towards new heights of excellence.
Innovative Dual Shaft Electric Motor Revolutionizes the Industry
Dual Shaft Electric Motor Revolutionizes the IndustryIn recent years, technological advancements have paved the way for major innovations in various sectors, including transportation, manufacturing, and renewable energy. These advancements have driven companies to develop more efficient and sustainable solutions to meet the evolving demands of consumers and the planet. One breakthrough that has garnered attention is the Dual Shaft Electric Motor, a game-changing invention that has the potential to revolutionize multiple industries.Developed by a leading research and engineering company, this revolutionary Dual Shaft Electric Motor is the result of years of dedicated research and development. It combines cutting-edge technology, advanced materials, and superior design to deliver unparalleled performance and efficiency. By removing the brand name, we allow the focus to be on the motor itself and the impact it can have on various sectors.The Dual Shaft Electric Motor boasts several key features that set it apart from traditional motors. One of its unique characteristics is its ability to operate with maximum efficiency in both low and high torque applications. This versatility makes it a suitable choice for a wide range of industries, from automotive to aerospace, where precise control and power are crucial.Another significant attribute of this motor is its compact and lightweight design. With its streamlined construction, it takes up less space and can be easily integrated into existing systems. As a result, manufacturers can optimize space utilization and enhance overall production efficiency.Furthermore, the Dual Shaft Electric Motor is designed to minimize energy consumption and reduce carbon emissions. By utilizing the latest advancements in electric motor technology, it significantly enhances energy efficiency compared to conventionally powered motors. This innovation aligns perfectly with the growing global emphasis on sustainability and the urgent need to address climate change.One industry that stands to benefit greatly from the integration of this motor is the automotive sector. With the world shifting towards electric vehicles (EVs) as a means to combat air pollution and reduce dependence on fossil fuels, the Dual Shaft Electric Motor offers an ideal solution. Its superior efficiency and power make it a perfect fit for electric cars, allowing for longer driving ranges and faster acceleration.Moreover, by partnering with automotive manufacturers, the introduction of this motor could catalyze the mass adoption of EVs. Its reliability, performance, and energy-saving capabilities can build consumer confidence in electric vehicles, accelerating the transition to a cleaner and more sustainable future.Beyond the automotive sector, the Dual Shaft Electric Motor has promising applications in several other industries. In aerospace, for example, it can revolutionize the performance and energy efficiency of aircraft, leading to reduced fuel consumption and lower operating costs. Similarly, in manufacturing, the motor's flexibility and precision control can optimize production processes, resulting in improved productivity and cost savings.Furthermore, this motor's silent operation and reduced maintenance requirements make it an ideal choice for numerous residential and commercial applications. From household appliances to HVAC systems, the Dual Shaft Electric Motor can improve energy efficiency and provide a quieter and more comfortable environment for users.The introduction of the Dual Shaft Electric Motor signifies a groundbreaking milestone in the pursuit of sustainable and efficient solutions. With its unique features and potential for transformative impact across various sectors, this motor is poised to revolutionize industries and contribute to a greener future. As the world embraces innovative technologies, it is essential for companies to embrace change and adapt to these new advancements in order to remain at the forefront of their respective industries.
High-Quality Hot Forging Yoke: What You Need to Know
Hot Forging Yoke: A Testament to Excellence in Metal Fabrication at []The process of hot forging has been a vital part of manufacturing for centuries. It involves heating metal to a high temperature and then shaping it through compressive forces to create intricate and durable parts. One such part that is crucial in various industries is the yoke, which is used in machinery and equipment for transmitting power and motion. When it comes to hot forging yokes, [] is a name that stands out for its excellence in metal fabrication.Established in [], [] has been at the forefront of hot forging technology, producing high-quality yokes for a wide range of applications. The company's commitment to precision engineering and quality control has earned them a reputation as a trusted supplier in the industry. With state-of-the-art facilities and a team of skilled professionals, [] has continually raised the bar for hot forging yokes, delivering products that meet the highest standards of performance and reliability.The hot forging process at [] begins with the careful selection of raw materials, ensuring that only the finest quality metal is used. The metal is then heated to a precise temperature to make it malleable, allowing it to be shaped with extreme precision. Using advanced forging equipment and techniques, the metal is formed into the desired yoke shape, taking into account the specific requirements of the customer. This meticulous approach to hot forging results in yokes that are not only dimensionally accurate but also possess excellent mechanical properties.One of the key advantages of hot forging yokes is the superior strength and durability they offer. The process of hot forging aligns the grain structure of the metal, making it extremely resistant to fatigue and impact. This makes hot forged yokes ideal for demanding applications where reliability is non-negotiable. Whether it's in the automotive, aerospace, or heavy machinery sector, []'s hot forged yokes have proven their mettle time and time again, performing flawlessly even under the most punishing conditions.In addition to strength, hot forging yokes from [] also boast excellent surface finish and dimensional consistency. This is crucial in ensuring trouble-free assembly and operation of the equipment they are used in. []'s dedication to precision and quality is evident in every yoke they produce, making them a preferred choice for OEMs and end-users alike.Furthermore, [] is committed to sustainability and environmental responsibility in its manufacturing processes. The company ensures that its hot forging operations comply with stringent environmental regulations, minimizing waste and energy consumption. By embracing eco-friendly practices, [] not only reduces its carbon footprint but also sets an example for the industry as a whole.As a customer-centric company, [] places great emphasis on understanding and fulfilling the unique requirements of its clients. The company works closely with customers to develop custom hot forged yokes that are tailored to their specific needs. From design and prototyping to full-scale production, [] offers comprehensive solutions that are aimed at delivering maximum value to its customers. This customer-focused approach, coupled with []'s technical expertise, has earned them the trust and loyalty of a diverse clientele.Looking ahead, [] continues to innovate and invest in the latest hot forging technologies to further enhance its capabilities. The company remains dedicated to pushing the boundaries of what is possible in metal fabrication, with a relentless pursuit of excellence in every aspect of its operations. With a solid track record of delivering top-notch hot forged yokes and a forward-looking approach, [] is poised to remain a leader in the industry for years to come.