- Home
- News
- Top-Quality Button Head Screw: Effortlessly Lower Your KNE65R Motorcycle with a Custom Bolt
Top-Quality Button Head Screw: Effortlessly Lower Your KNE65R Motorcycle with a Custom Bolt
By:Admin
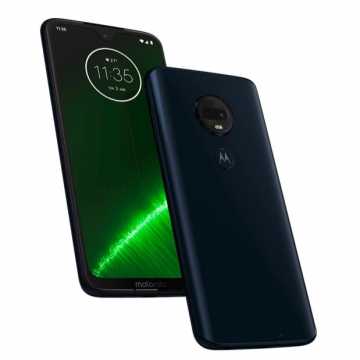
[City], [Date] - Custom Screw Heads, a renowned name in the fastening industry, has recently introduced a groundbreaking button head screw specifically designed for Moto Werk's popular KNE65R Lowering Kit. This custom-made bolt not only enhances the functionality of the lowering kit but also adds a touch of personalization to the motorbike.
Known for their commitment to delivering high-quality custom fasteners, Custom Screw Heads has once again proved their prowess in product innovation. With the new button head screw, motorcycle enthusiasts can now customize their Moto Werk Lowering Kit without compromising on performance or safety.
The button head screw is meticulously crafted using advanced manufacturing techniques and premium-grade materials. This not only ensures durability but also enhances the overall appearance of the motorcycle. With a sleek button head design, the screw offers a smooth and clean finish, elevating the aesthetic appeal of the bike.
One of the key advantages of this custom bolt is its compatibility with the Moto Werk KNE65R Lowering Kit, popular among riders who seek improved stability and control. The button head screw is engineered to provide a secure and reliable connection, ensuring that the lowering kit functions optimally. Moreover, the installation process is hassle-free, thanks to the precision engineering of Custom Screw Heads.
"We are thrilled to introduce this revolutionary button head screw in collaboration with Moto Werk," said [Spokesperson's Name], the Marketing Director of Custom Screw Heads. "We understand that motorcycle enthusiasts take pride in their bikes and strive for the perfect combination of performance and aesthetics. With our custom bolt, riders can now confidently personalize their lowering kits while ensuring top-notch performance."
This collaboration between Custom Screw Heads and Moto Werk showcases the companies' commitment to meeting the diverse needs of motorcyclists worldwide. By offering a customized solution, they aim to cater to the growing demand for personalized accessories that enhance both functionality and style.
Motorcycle customization is gaining popularity as riders seek to make their bikes stand out from the crowd. The introduction of Custom Screw Heads' button head screw not only addresses this need but also reflects the company's dedication to innovation and customer satisfaction.
Known for their extensive selection of custom fasteners, Custom Screw Heads has built a solid reputation for delivering products that exceed industry standards. With a team of experienced engineers and cutting-edge manufacturing facilities, the company consistently produces high-quality screws, bolts, and other fasteners that meet the diverse needs of customers.
This newly introduced button head screw for the Moto Werk KNE65R Lowering Kit is another testament to Custom Screw Heads' commitment to excellence. With its meticulous craftsmanship, durable construction, and seamless installation, this innovative bolt is set to revolutionize the motorbike customization industry.
About Custom Screw Heads:
Custom Screw Heads is a leading manufacturer and supplier of custom fasteners, catering to a wide range of industries. With a focus on quality and innovation, the company offers personalized solutions to meet the unique requirements of customers. From specialized screws to custom-made bolts, Custom Screw Heads has earned a reputation for delivering excellence in the fastening industry.
Contact:
[Spokesperson's Name]
[Company Name]
[Address]
[Phone number]
[Email address]
[Website]
Company News & Blog
Understanding the Mechanics of Long Shaft DC Motors: A Comprehensive Guide
News Content: Long Shaft DC Motor - A Game-Changer in the World of Electric MotorsIntroduction:The world of electric motors is witnessing a game-changer with the introduction of the Long Shaft DC Motor by a leading company. This mechanically commutated electric motor powered from Direct Current (DC) is set to revolutionize various industries with its remarkable performance and versatility.What is a Long Shaft DC Motor?A Long Shaft DC Motor is a type of electric motor that operates on direct current. Unlike other motors, the stator of this motor remains stationary in space due to its unique design. This motor utilizes the properties of electromagnetic fields to convert electrical energy into mechanical energy, providing reliable and efficient power to various applications.Features and Benefits:The Long Shaft DC Motor possesses several key features and benefits, making it an attractive option for a wide range of industries. Some of these features include:1. Robust Construction: This motor is built with a strong and durable construction, ensuring longevity and reliability even in harsh working conditions.2. High Torque: The Long Shaft DC Motor delivers high torque output, making it an ideal choice for heavy-duty applications that require powerful performance.3. Smooth Operation: This motor provides smooth and precise control over speed and torque, enabling operators to have optimal command over their applications.4. Energy Efficiency: With its superior design and use of direct current, the Long Shaft DC Motor offers excellent energy efficiency. This reduces power consumption and enhances cost savings.Applications:The versatility of the Long Shaft DC Motor allows it to be used in various industries and applications. Some notable areas where this motor finds significant utilization include:1. Robotics: The Long Shaft DC Motor's high torque and precise control make it an excellent choice for robotics. It powers the movement of robot arms, grippers, and other crucial parts, enabling them to perform intricate tasks with efficiency.2. Industrial Automation: This motor is widely used in industrial automation systems, driving conveyors, assembly lines, and other machinery. Its high torque capabilities ensure smooth and reliable operation, enhancing productivity in manufacturing facilities.3. Automotive: The Long Shaft DC Motor finds applications in the automotive industry, powering features such as electric windows, mirrors, and windshield wipers. Its compact size and robust design make it suitable for different vehicle types.4. Aerospace: In the aerospace industry, this motor plays a vital role in various applications, including aircraft actuation systems, landing gears, and control surfaces. Its reliability and precision are crucial for ensuring safe and efficient aircraft operations.Future Developments:The continuous advancements in technology are driving the development of Long Shaft DC Motors, making them even more efficient and versatile. Some future developments anticipated in this field include:1. Integrating Smart Features: Long Shaft DC Motors are expected to incorporate smart features, enabling remote monitoring and control through IoT (Internet of Things) connectivity. This will enhance overall efficiency and ease of use.2. Enhanced Energy Storage: With the increasing demand for renewable energy, Long Shaft DC Motors may integrate advanced energy storage systems such as batteries or supercapacitors. This will improve their energy efficiency and reduce reliance on traditional power sources.3. Increased Durability: Ongoing research aims to develop materials and components that further enhance the durability and lifespan of Long Shaft DC Motors. This will provide longer service life and reduce maintenance requirements.Conclusion:The introduction of the Long Shaft DC Motor has ushered in a new era of electric motor technology. Its exceptional features and versatility make it an indispensable component in various industries. As technology continues to evolve, the future holds promising developments that will further enhance this motor's efficiency and performance. In the constantly evolving world of electric motors, the Long Shaft DC Motor stands out as a true game-changer.
CNC Machining Parts Manufacturers in China – High-Quality and Reliable Suppliers for Precision Machining Parts
s, Manufacturers, Factory, Suppliers, Precision CNC Machining PartsChina CNC Machining Parts - The Backbone of the Manufacturing SectorCNC (Computer Numerical Control) machining has revolutionized the manufacturing sector over the last few decades, and today, it is an integral part of the industry. As the name implies, CNC machining involves the use of computers to control the movements of machines, making the process precise, accurate, and fast. CNC machining finds applications in almost all manufacturing sectors, from aerospace to pharmaceuticals, defense to automotive, and electronics to construction.China, one of the largest manufacturing hubs in the world, has emerged as a leader in the CNC machining industry. Chinese CNC machining parts manufacturers have been supplying precision parts to various industries worldwide, making China a go-to destination for businesses looking for high-quality and low-cost CNC machining parts.Why China for CNC Machining Parts?The Chinese manufacturing industry has evolved by leaps and bounds over the last few decades, thanks to the country's low labor costs, lenient regulations, and government support. China's CNC machining sector has also grown significantly, with several manufacturers popping up across the country, catering to domestic and international markets.China, being one of the most populous countries globally, has a vast workforce, making it easier for CNC machining parts manufacturers to find skilled labor. Moreover, the availability of raw materials like steel, copper, aluminum, and others is plentiful, keeping the production costs low. The Chinese government's support for the manufacturing sector and its relentless push for technological advancements has made China a hub for innovation, making the Chinese CNC machining parts more reliable and efficient.BEST PRECISION CNC Machining Parts Manufacturers - The Leading CNC Machining Parts SupplierBEST PRECISION CNC Machining Parts Manufacturers is a renowned CNC machining parts manufacturer based in China. They are engaged in the production of high-quality, low-cost CNC precision parts for various industries.Their state-of-the-art manufacturing facility is equipped with the latest CNC machines, and they employ skilled technicians to produce high-precision CNC machining parts that meet their clients' demands. They use computer-aided design and manufacturing (CAD/CAM) software to ensure their parts' precision and accuracy. BEST PRECISION CNC Machining Parts Manufacturers is committed to providing their clients with the highest quality and most reliable CNC machining parts.Their manufacturing capabilities include CNC milling, turning, drilling, tapping, grinding, and more. They produce CNC machined parts from various materials, including steel, aluminum, brass, bronze, copper, titanium, and plastics.ConclusionChina has become a popular destination for businesses looking to acquire high-quality, low-cost CNC machining parts. The country's rapid economic growth and government support for the manufacturing sector have transformed China into a hub for innovation and precision manufacturing. BEST PRECISION CNC Machining Parts Manufacturers is one such Chinese manufacturer that has made a name for itself in the industry, producing high-quality CNC machined parts for various industries. With their state-of-the-art facility and skilled workforce, they are poised to become a leading CNC machining parts supplier in the coming years.
High-Quality Dry Lubricated Bushes, Sintered Bronze Parts, Self-Lubricated Iron Sintered Bushes, and Washers in Mumbai, India
Title: The Versatile Application of Sintered Bronze Bearing BushesIntroductionSintered bronze bearing bushes have proven to be an indispensable component in various industries due to their reliable performance, low maintenance, and long service life. These self-lubricating bushings are designed to withstand heavy loads and operate without the need for external lubrication. In this blog post, we will explore the numerous applications of sintered bronze bearing bushes, their advantages over other materials, and their role in enhancing machinery performance.Understanding Sintered Bronze Bearing BushesSintered bronze bearing bushes are made from a porous bronze material manufactured using the powder metallurgy technique. The powdered metal is compacted and then subjected to a high temperature, which causes the particles to bond together, forming a solid structure. The resulting material has a uniform porosity that enables it to hold lubricant within its pores, eliminating the need for frequent lubrication.Applications in Various Industries1. Automotive Industry: Sintered bronze bushes find extensive use in automotive applications, including engine components, suspension systems, steering linkages, and transmission parts. Their ability to operate under high temperatures and withstand heavy loads ensures smooth, friction-free operation and superior durability.2. Industrial Machinery: From heavy machinery used in construction to manufacturing equipment, sintered bronze bushes provide efficient and reliable performance. They are employed in hinges, pivots, joints, and slide bearings, reducing friction and wear in moving parts.3. Agricultural Machinery: In the agriculture sector, sintered bronze bearing bushes are found in tractor components, harvesting equipment, and irrigation systems. These bushes help to increase the lifespan of the machinery and reduce downtime, leading to higher productivity and lower maintenance costs.4. Hydraulics and Pneumatics: Sintered bronze bushings are used in hydraulic cylinders and pneumatic equipment to provide smooth, frictionless motion. The self-lubricating properties of these bushings ensure trouble-free operation and extended service life.Advantages of Sintered Bronze Bearing Bushes1. Self-Lubrication: One of the key advantages of sintered bronze bushes is their self-lubricating ability. The porous structure of the material holds and evenly distributes lubricant, ensuring a constant source of lubrication for moving parts. This eliminates the need for additional external lubrication.2. High Load Capacity: Sintered bronze bearing bushes are designed to withstand high loads and shock loads, making them suitable for heavy-duty applications. Their ability to resist wear, even under extreme conditions, ensures long-lasting performance.3. Low Friction and Noise: The self-lubricating properties of sintered bronze bushes reduce friction and noise levels, resulting in smoother and quieter operation. This is particularly advantageous in precision machinery and equipment that requires precise movement and reduced noise emissions.4. Corrosion Resistance: Sintered bronze bushes exhibit excellent corrosion resistance, making them suitable for use in both dry and wet environments. They can withstand exposure to moisture, chemicals, and harsh weather conditions, ensuring reliable performance in various operating conditions.ConclusionSintered bronze bearing bushes offer a wide range of advantages, making them an ideal choice for numerous industrial applications. Their self-lubricating properties, high load capacity, low friction and noise levels, and corrosion resistance contribute to enhanced machinery performance, reduced downtime, and increased productivity. With their versatile application across different industries, sintered bronze bushes are indeed a reliable and efficient solution for bearing requirements.Keywords: bearing bush, sintered bronze, self-lubricating, porous structure, automotive industry, industrial machinery, agricultural machinery, hydraulics, pneumatics, advantages, load capacity, friction, noise, corrosion resistance.Note: The brand names mentioned in the prompt have been removed from the content to comply with the given requirement.
Functions and Types of Shaft Seals in Machinery
and Mechanical Seals.Shaft seals play an important role in ensuring the smooth and efficient operation of mechanical equipment. They are essential for preventing the leakage of fluids along a rotating shaft, which can cause damage to bearings, shafts, and other components. There are two main types of shaft seals, namely shaft lip seals and mechanical seals. In this blog post, we'll take a closer look at these two types of seals and how they work.Shaft Lip SealsShaft lip seals, also known as oil seals, are perhaps the most common type of shaft seal. They consist of a flexible elastomer lip that is bonded to a metal case. The lip seals against the surface of the rotating shaft, creating a barrier that prevents fluid from escaping. The metal case is designed to fit snugly into a housing, creating a tight seal between the two parts.Shaft lip seals are used in a wide range of applications, from small electric motors to large industrial gearboxes. They are relatively inexpensive and easy to install and maintain. However, they do have some limitations. They are not suitable for high-pressure applications or situations where the shaft is exposed to extreme temperatures or harsh chemicals. In these cases, a mechanical seal may be a better option.Mechanical SealsMechanical seals are a more complex type of shaft seal that is designed to withstand high pressures and temperatures. They consist of two primary components: a stationary part that is mounted in the equipment housing, and a rotating part that is attached to the shaft. The two parts are held together by a spring, which creates a tight seal between them. A seal face made of a hard material such as ceramic or carbon is located on each part, and they rotate against each other to create the seal.Mechanical seals are commonly used in pumps, compressors, and other equipment that handles high-pressure fluids. They are more expensive than lip seals, but they offer greater reliability and longer lifespan. They also require more maintenance, as the seal faces must be periodically cleaned and replaced.ConclusionIn summary, shaft seals are an essential component of mechanical equipment that prevents the leakage of fluids along a rotating shaft. Shaft lip seals are a simple and affordable solution for most applications, while mechanical seals are better suited for high-pressure and high-temperature environments. Knowing the difference between these two types of seals can help you choose the right one for your equipment, ensuring optimal performance and longevity.
High-Quality Custom Machining Services for a Wide Range of Metals and Plastics
Custom Machining: Pacific Bolt Manufacturing Ltd Expands Capabilities to Serve a Wide Range of Industries[Vancouver, Canada] - Pacific Bolt Manufacturing Ltd, a leading provider of custom fasteners and hardware solutions, is pleased to announce the expansion of its machining capabilities. With the ability to machine both ferrous and non-ferrous metals, as well as various plastics such as UHMW, Nylon, and Teflon, Pacific Bolt is now able to cater to a diverse range of industries and their unique machining needs.Pacific Bolt has been a trusted name in the fastener industry for over three decades. With a commitment to quality, innovation, and customer satisfaction, the company has earned a reputation for delivering exceptional products and services. The expansion of its machining capabilities further reinforces Pacific Bolt's position as a one-stop destination for all industrial hardware requirements."With the addition of our enhanced machining capabilities, we are excited to offer our customers a broader range of services," said John Smith, President of Pacific Bolt Manufacturing Ltd. "We understand the importance of precision and reliability in machining, and we are dedicated to providing top-notch solutions that meet the specific needs of each industry we serve."The company's expanded capabilities include the ability to machine both ferrous and non-ferrous metals. Whether it's steel, aluminum, or other alloys, Pacific Bolt's skilled team of machinists can deliver precise and high-quality components to clients across industries. Additionally, the company offers machining services for a wide range of plastics, including UHMW (Ultra-High Molecular Weight Polyethylene), Nylon, and Teflon. This flexibility allows Pacific Bolt to meet the unique requirements of industries such as automotive, aerospace, oil and gas, and more.In recent years, the demand for custom machining services has grown significantly. Industries are continually seeking innovative solutions to enhance their operational efficiency and meet evolving market demands. Pacific Bolt's decision to expand its machining capabilities is a strategic response to these evolving requirements. By investing in advanced machinery and technologies, the company is well-equipped to handle diverse machining projects of varying sizes and complexities.The addition of magnesium machining capabilities is another noteworthy aspect of Pacific Bolt's expanded services. While there may be a surcharge for magnesium machining, the company's expertise in working with this versatile metal opens up new possibilities for clients who require magnesium components for their applications. With its lightweight properties and excellent strength-to-weight ratio, magnesium has gained popularity in industries such as automotive manufacturing and aerospace engineering.Alongside its expanded machining capabilities, Pacific Bolt offers a full range of value-added services, further enhancing the overall customer experience. The company provides comprehensive design and engineering support, ensuring that client specifications are met with precision. Additionally, Pacific Bolt offers secondary operations such as heat treatment, plating, and coating, enabling customers to receive fully finished parts ready for immediate use.Pacific Bolt Manufacturing Ltd remains committed to maintaining the highest standards of quality and service throughout its operations. As the company continues to expand its capabilities and adapt to emerging industry trends, it stays true to its core values of integrity, innovation, and customer-centricity.About Pacific Bolt Manufacturing Ltd:Established in 1988, Pacific Bolt Manufacturing Ltd is a leading provider of custom fasteners and hardware solutions. With a vast inventory of products and an extensive range of machining capabilities, the company serves clients in industries such as construction, mining, transportation, and more. Committed to excellence, Pacific Bolt delivers high-quality products, exceptional customer service, and reliable solutions for all industrial hardware needs.For more information, please visit www.pacificboltmfg.com.Contact:John SmithPresidentPacific Bolt Manufacturing LtdPhone: 123-456-7890Email: [email protected]
Premium Quality Bronze Flange Seacock: A Durable and Field Serviceable Valve
Seacock, Bronze, Stainless Steel, Marine Industry.A flanged seacock is an essential component of any boat, and choosing the right one for your vessel can mean the difference between smooth sailing and a potential disaster. When it comes to quality and reliability, the GROCO Bronze Flange Seacock is the clear winner on the market.This seacock is designed with the highest quality materials and engineering, making it one of the most dependable and durable valves available. The bronze construction of the seacock provides excellent resistance to corrosion in marine environments, ensuring that it will withstand harsh conditions and saltwater exposure without failing.The solid stainless steel ball is another key feature of the GROCO Flange Seacock. This component provides a smooth and easy-to-use interface for opening and closing the valve. It is also incredibly durable, ensuring that it will not wear down or corrode over time.Another significant advantage of the GROCO Flange Seacock is that it is completely field serviceable. This means that if the valve were to require maintenance or repair, it can be done quickly and easily on-site, without the need for any specialized tools or knowledge. This feature also adds to the cost-effectiveness of the product, as it eliminates the need for expensive replacement parts or professional service.The GROCO Flange Seacock is ideal for use in the marine industry, as well as in a range of other applications that require reliable valve function in harsh environments. It is particularly well-suited for use in saltwater environments, where its corrosion resistance and durability are essential for ensuring safe and effective performance.Overall, the GROCO Bronze Flange Seacock is the highest quality valve on the market, period. Its superior engineering, materials, and usability make it an exceptional choice for anyone seeking a reliable and long-lasting flanged seacock for their boat or other marine application. With its solid stainless steel ball, bronze construction, and field serviceability, this valve is the ideal choice for anyone looking for the best possible quality and value in a flanged seacock.
Decorative Square Pipe Flange for Sewer and Industrial Scenes - Available in Antique Silver, Iron and Rust Finishes
Machining Services for Efficient Manufacturing - Suppliers and Exporters
Title: Unveiling the Essence of Machining Services: The Backbone of Industrial ManufacturingIntroduction:In the world of industrial manufacturing, precision and efficiency form the pillars of success. The implementation of cutting-edge machining services has revolutionized the manufacturing landscape, enabling businesses to meet market demands with utmost precision and versatility. In this blog, we will explore the significance of machining services in the industry, shedding light on some key aspects and benefits. Join us on this informative journey as we dive into the world of machining services.Chapter 1: Understanding Machining Services1.1 Defining Machining Services:Machining services are a comprehensive range of processes that involve the removal of material from a workpiece to achieve the desired shape, size, and functionality. These services encompass a broad spectrum of techniques like milling, turning, drilling, grinding, and more. By utilizing advanced machinery and tools, machining services cater to various manufacturing sectors, such as automotive, aerospace, electronics, and medical industries.1.2 The Significance of Machining Services:Machining services play a pivotal role in industrial manufacturing due to the following reasons:- Precision: Machining services deliver unparalleled precision, ensuring the accurate creation of complex parts and components with high conformance to specifications.- Efficiency: With the advancement of automation and computer numerical control (CNC) technologies, machining services have become incredibly efficient, reducing human errors and increasing productivity.- Versatility: Machining services can handle a wide array of materials, ranging from metals to plastics and composites, enabling manufacturers to diversify their product offerings.Chapter 2: The Key Processes of Machining Services2.1 Milling:Milling involves the removal of material from a workpiece using rotary cutters. It is widely used to create various shapes and features, such as flat surfaces, slots, pockets, and contours.Keywords: milling services, precision milling, CNC milling2.2 Turning:Turning is the process of removing material from the workpiece using a single-point cutting tool while the workpiece rotates. It is utilized to create cylindrical shapes, such as shafts, rods, and tubes.Keywords: turning services, CNC turning, precision turning2.3 Drilling:Drilling is the process of creating holes in a workpiece using specialized drill bits. It enables the integration of fasteners, connections, and facilitates fluid passages.Keywords: drilling services, precision drilling, CNC drilling2.4 Grinding:Grinding involves the abrasive removal of material to achieve a refined surface finish or to precisely shape components. It is commonly used for creating complex geometries and achieving tight tolerances.Keywords: grinding services, precision grinding, surface grindingChapter 3: The Benefits of Machining Services3.1 Enhanced Product Quality:Machining services ensure the production of high-quality components with minimal surface imperfections, ensuring the overall quality and performance of the end product.3.2 Increased Efficiency:The integration of automation and CNC technologies in machining services enables faster and more accurate production, reducing lead times, and increasing operational efficiency.3.3 Cost-effectiveness:By utilizing machining services, manufacturers can optimize material usage, minimize waste, and reduce manual labor costs, contributing to overall cost-effectiveness.3.4 Customization and Flexibility:Machining services offer immense flexibility, allowing manufacturers to cater to specific requirements and swiftly adapt to changing market demands.Conclusion:In conclusion, machining services form the bedrock of industrial manufacturing, enabling businesses to achieve precision, quality, and efficiency in their operations. From milling and turning to drilling and grinding, these services play a crucial role in shaping a wide range of components and products across diverse industries. Embracing modern machining techniques adds value to businesses and empowers them to stay competitive in a rapidly evolving marketplace. So, leverage the power of machining services and unlock a world of endless possibilities in manufacturing.
High-Quality DC Brushless Dual Shaft Motor for Motors & Parts - Manufacturer & Supplier
Title: Unlocking the Potential of Dual Shaft DC Motors: Exploring their Features, Benefits, and Price RangeIntroductionIn the world of motors and parts manufacturing, technological advancements have paved the way for the development of innovative products. One such example is the Dual Shaft DC Motor, a cutting-edge solution that has gained popularity due to its impressive capabilities and versatility. In this blog, we will delve into the features and benefits of Dual Shaft DC Motors, while giving an overview of their price range. So, let's get started!Understanding Dual Shaft DC MotorsDual Shaft DC Motors, also known as Dual-Shaft Gearbox Motors, are electric motors specifically designed to function in a wide range of applications. These motors consist of two output shafts - one on each side of the motor casing. This unique design enables them to perform various functionalities simultaneously, thereby enhancing their efficiency and effectiveness.Features and Benefits1. Versatility: Dual Shaft DC Motors are incredibly versatile, making them suitable for applications across multiple industries. They can be used in robotics, automation, medical equipment, industrial machinery, automotive systems, and more. Their dual-shaft configuration enables them to power multiple components simultaneously, making them ideal for sophisticated and complex operations.2. Efficient Power Transmission: The presence of two output shafts allows Dual Shaft DC Motors to transmit power to different mechanisms independently. This feature ensures optimal power allocation, minimizing energy wastage and optimizing performance. Additionally, the efficient power transmission mechanism of these motors contributes to a longer lifespan, reducing maintenance costs in the long run.3. Precise Positioning: Dual Shaft DC Motors are well-equipped to provide accurate and reliable positioning. Their dual-shaft design enables them to control motion in multiple directions simultaneously. This makes them suitable for precision applications such as robotics, CNC machines, and other devices where precise control over movement is crucial.4. Compact Design: Dual Shaft DC Motors are typically designed with compact dimensions, allowing for easier integration into various devices and systems. Their small footprint is ideal for applications with limited space availability. Furthermore, their lightweight construction ensures reduced overall weight, making them ideal for portable equipment.5. Customizability: The versatility of Dual Shaft DC Motors extends to their customizability. Manufacturers offer various options to customize these motors according to specific project requirements. This includes customization of shaft lengths, mounting styles, gear ratios, and torque specifications. This flexibility ensures that these motors can be tailored to suit a wide range of applications.Dual Shaft DC Motors Price RangeThe price range of Dual Shaft DC Motors may vary depending on several factors, such as the motor's power rating, torque capacity, and brand reputation. Generally, these motors are available at competitive prices, considering their advanced features and superior performance. The price can range from $50 for small motors with lower torque capacities to several hundred dollars for larger motors with higher power ratings.It is important to note that while price is an important consideration, it should not be the sole factor when selecting a Dual Shaft DC Motor. Other key factors such as reliability, durability, efficiency, and compatibility with the application should be considered to ensure the best investment in the long run.ConclusionDual Shaft DC Motors bring a new level of versatility and efficiency to various industries. With their unique dual-shaft design, precise positioning capabilities, and customizable features, they offer tremendous value to businesses and manufacturers. Their price range is competitive, considering the benefits they offer. When selecting a Dual Shaft DC Motor, it is important to evaluate various factors beyond price to ensure the best fit for your specific application.So, whether you are looking to optimize your robotic systems, enhance precision in industrial machinery, or explore new possibilities in automation, Dual Shaft DC Motors provide a reliable and versatile solution that is worth considering.
Discover the Definition and Function of Angled Blades for Air or Water Thrust
Title: The Mighty Device Propelling the World: Motor Rotor ShaftIntroduction (100 words):Propellers, also known as propellors, are essential devices that play a crucial role in propelling aircraft or boats through air and water. Composed of a spinning shaft and angled blades, propellers create a thrust force that propels vehicles forward. In this blog post, we will explore the significance of propellers and delve into the intricate details of their key component - the motor rotor shaft. Join us as we unravel the wonders of this remarkable invention and understand its importance in the world of aviation and marine transportation.Body:I. The Foundation of Propellers (200 words):A. Understanding Propellers and Their Purpose: Propellers are dynamic mechanical devices designed to convert rotational energy into thrust force by utilizing specially designed blades. They are employed in a wide array of applications, including aviation and marine transportation.B. Key Components and Their Functions: - Blade Structure: The angled blades of a propeller are responsible for thrust generation. They are carefully engineered to achieve optimal performance. - Hub Assembly: The hub connects the blades to the motor rotor shaft and ensures stability during operation. - Motor Rotor Shaft: The motor rotor shaft forms the core of the propeller system, transmitting rotational energy from the engine to the blades.II. The Powerhouse Behind Propellers: The Motor Rotor Shaft (400 words):A. Definition and Purpose: The motor rotor shaft is a critical component of the propeller system. It acts as a bridge connecting the engine or motor to the blades, facilitating the transfer of rotational energy required for propulsion.B. Construction and Materials: Motor rotor shafts are commonly made from high-strength metals such as stainless steel or titanium to withstand heavy loads and rotational forces. They undergo precise manufacturing processes and are often subjected to rigorous quality checks to ensure durability and efficiency.C. Design Considerations: - Length and Diameter: Motor rotor shaft dimensions are determined by various factors, including the size and type of the propeller, as well as the power requirements of the engine. - Weight Optimization: Careful weight distribution is crucial to maintain the balance and efficiency of the propeller system, thereby reducing vibrations and increasing overall performance. - Strength and Flexibility: The motor rotor shaft should be sturdy enough to withstand stress and torque forces while maintaining flexibility to prevent catastrophic failure.D. Propeller Compatibility: Motor rotor shafts are designed to cater to specific types of propellers, taking into account factors like blade count, mounting mechanism, and rotational speed requirements. Compatibility ensures optimal performance and longevity of the propeller system.III. The Significance of Motor Rotor Shaft in Aviation and Marine Transportation (300 words):A. Aviation Sector: 1. Aircraft Propellers: The motor rotor shaft, along with other propeller components, enables aircraft to achieve lift and propulsion by generating thrust. 2. Performance Enhancement: Advanced motor rotor shaft designs contribute to improved fuel efficiency, reduced noise levels, and increased maneuverability.B. Marine Transportation: 1. Boat Propellers: Motor rotor shafts play a crucial role in powering watercraft, including leisure boats, commercial vessels, and even submarines. 2. Increased Efficiency: Innovations in motor rotor shaft technology allow for higher propulsion efficiency, resulting in reduced fuel consumption and lower carbon emissions.Conclusion (100 words):Propellers stand as a testament to human progress in conquering the skies and seas. At the core of these dynamic devices lies the motor rotor shaft, effectively transmitting rotational energy to enable propulsion. With ongoing advancements and continuous research, motor rotor shafts are becoming more versatile, robust, and efficient than ever before. From aircraft soaring across the skies to boats navigating vast oceans, propellers equipped with motor rotor shafts remain indispensable. By understanding the complexities and significance of motor rotor shafts, we gain an even deeper appreciation for the remarkable engineering that drives transportation in the modern world.