High-Quality Lip Seals for Shaft Applications: What You Need to Know
By:Admin
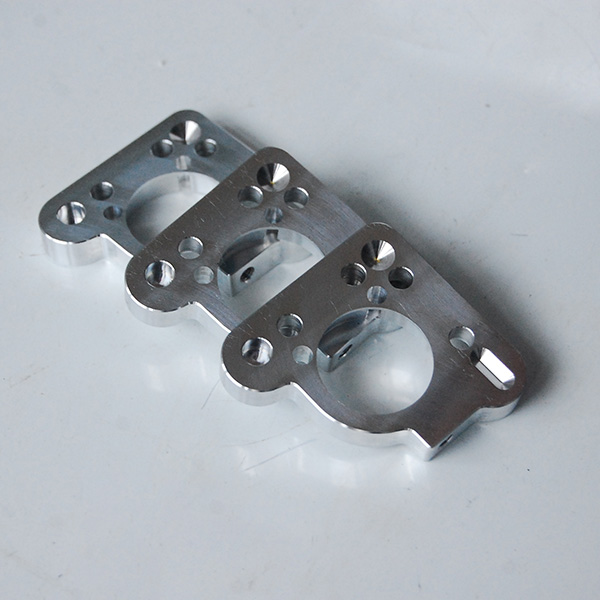
Shaft Lip Seals, also known as rotary shaft seals or oil seals, are essential components in various industrial applications. These seals are designed to prevent the leakage of lubricants and fluids from rotating or stationary shafts. With their crucial role in maintaining the efficiency and reliability of machinery and equipment, the quality and performance of shaft lip seals are of utmost importance.
{Company Name}, a leading manufacturer of sealing solutions, is dedicated to delivering high-quality products that meet the demanding requirements of the industry. With a strong focus on innovation, reliability, and performance, {Company Name} has established a reputation for excellence in providing sealing solutions for a wide range of applications.
The key to the exceptional performance of {Company Name}'s shaft lip seals lies in their advanced design and superior materials. These seals are engineered to withstand the harsh conditions of various industrial environments, including high pressures, extreme temperatures, and aggressive media. By utilizing the latest in sealing technology and materials science, {Company Name} ensures that its shaft lip seals deliver long-lasting performance and protection for the equipment they are used in.
One of the key features of {Company Name}'s shaft lip seals is their ability to provide effective sealing under challenging operating conditions. Whether it's in heavy-duty machinery, automotive applications, or industrial equipment, these seals are designed to maintain a reliable barrier against contaminants and prevent the loss of lubricants and fluids. This not only helps to extend the service life of the equipment but also contributes to its overall performance and efficiency.
In addition to their exceptional sealing performance, {Company Name}'s shaft lip seals are designed for easy installation and maintenance. With a range of standard sizes and custom solutions available, these seals can be tailored to meet the specific requirements of different applications. This flexibility, combined with the company's expertise in sealing technology, ensures that customers can rely on {Company Name} to provide the right sealing solution for their needs.
Furthermore, {Company Name} takes pride in its commitment to quality and customer satisfaction. The company's manufacturing processes are subject to rigorous quality control measures, ensuring that each seal meets the highest standards of performance and reliability. By maintaining a strong focus on quality assurance, {Company Name} has earned the trust of customers who rely on its sealing solutions for their critical applications.
As the industry continues to evolve, {Company Name} remains at the forefront of sealing technology, constantly pushing the boundaries of innovation and performance. The company's research and development efforts are focused on developing new sealing solutions that address the evolving needs of the industry, whether it's in terms of environmental regulations, energy efficiency, or reliability.
In conclusion, {Company Name} is a trusted name in the field of sealing solutions, and its shaft lip seals are a testament to its commitment to excellence. With a focus on quality, performance, and innovation, {Company Name} continues to provide reliable sealing solutions that meet the demanding requirements of various industrial applications. As the industry looks towards the future, {Company Name} is poised to continue its legacy of delivering high-quality sealing solutions that help to drive the efficiency and reliability of machinery and equipment.
Company News & Blog
CNC Machining Parts Manufacturers in China – High-Quality and Reliable Suppliers for Precision Machining Parts
s, Manufacturers, Factory, Suppliers, Precision CNC Machining PartsChina CNC Machining Parts - The Backbone of the Manufacturing SectorCNC (Computer Numerical Control) machining has revolutionized the manufacturing sector over the last few decades, and today, it is an integral part of the industry. As the name implies, CNC machining involves the use of computers to control the movements of machines, making the process precise, accurate, and fast. CNC machining finds applications in almost all manufacturing sectors, from aerospace to pharmaceuticals, defense to automotive, and electronics to construction.China, one of the largest manufacturing hubs in the world, has emerged as a leader in the CNC machining industry. Chinese CNC machining parts manufacturers have been supplying precision parts to various industries worldwide, making China a go-to destination for businesses looking for high-quality and low-cost CNC machining parts.Why China for CNC Machining Parts?The Chinese manufacturing industry has evolved by leaps and bounds over the last few decades, thanks to the country's low labor costs, lenient regulations, and government support. China's CNC machining sector has also grown significantly, with several manufacturers popping up across the country, catering to domestic and international markets.China, being one of the most populous countries globally, has a vast workforce, making it easier for CNC machining parts manufacturers to find skilled labor. Moreover, the availability of raw materials like steel, copper, aluminum, and others is plentiful, keeping the production costs low. The Chinese government's support for the manufacturing sector and its relentless push for technological advancements has made China a hub for innovation, making the Chinese CNC machining parts more reliable and efficient.BEST PRECISION CNC Machining Parts Manufacturers - The Leading CNC Machining Parts SupplierBEST PRECISION CNC Machining Parts Manufacturers is a renowned CNC machining parts manufacturer based in China. They are engaged in the production of high-quality, low-cost CNC precision parts for various industries.Their state-of-the-art manufacturing facility is equipped with the latest CNC machines, and they employ skilled technicians to produce high-precision CNC machining parts that meet their clients' demands. They use computer-aided design and manufacturing (CAD/CAM) software to ensure their parts' precision and accuracy. BEST PRECISION CNC Machining Parts Manufacturers is committed to providing their clients with the highest quality and most reliable CNC machining parts.Their manufacturing capabilities include CNC milling, turning, drilling, tapping, grinding, and more. They produce CNC machined parts from various materials, including steel, aluminum, brass, bronze, copper, titanium, and plastics.ConclusionChina has become a popular destination for businesses looking to acquire high-quality, low-cost CNC machining parts. The country's rapid economic growth and government support for the manufacturing sector have transformed China into a hub for innovation and precision manufacturing. BEST PRECISION CNC Machining Parts Manufacturers is one such Chinese manufacturer that has made a name for itself in the industry, producing high-quality CNC machined parts for various industries. With their state-of-the-art facility and skilled workforce, they are poised to become a leading CNC machining parts supplier in the coming years.
Experts Predict Strong Growth for Welded Steel Tube Market in the Next Decade
Title: Steel Welded Tube Manufacturer Revolutionizes Industry with Cutting-Edge TechnologyIntroduction:In the fast-paced world of industrial manufacturing, the need for high-quality and durable products has never been more essential. {Company Name}, a leader in the steel welded tube industry, has emerged as a trailblazer, revolutionizing the sector with their state-of-the-art technology and commitment to excellence. With a relentless focus on innovation, {Company Name} has solidified its position as a trusted manufacturer, providing its customers with superior steel welded tubes that meet and exceed industry standards.1. Innovative Technology Leads to Unparalleled Quality (150 words)With a deep understanding of the importance of technology in modern manufacturing, {Company Name} has invested heavily in advanced machinery and software systems that optimize the production process. By employing cutting-edge welding technologies, such as laser welding and automated systems, {Company Name} ensures the precision and consistency of their steel welded tubes. This not only enhances the overall quality of the products but also reduces production time and minimizes errors.The company's commitment to innovation extends to its research and development division, which continually explores new techniques and materials. By staying at the forefront of technological advancements, {Company Name} can deliver steel welded tubes that are not only stronger and more durable but also lightweight, making them more efficient and cost-effective for a variety of industrial applications.2. Superior Materials for Enhanced Performance (150 words)Recognizing the critical role that materials play in the functionality and longevity of steel welded tubes, {Company Name} sources only the highest-grade steel. Through stringent quality control measures, the company ensures that every tube meets rigorous standards, surpassing the expectations of customers across various industries.{Company Name} offers a diverse range of steel grades, including carbon steel, stainless steel, and alloy steel, to cater to different requirements. These materials boast excellent mechanical properties, corrosion resistance, and heat resistance, making them well-suited for applications in construction, automotive, energy, and more.Moreover, the welding technique employed by {Company Name} ensures the molecular integrity and strength of the welded joints, thereby eliminating weak points that are susceptible to failure or damage. This superior construction technique enhances the overall performance and durability of the steel welded tubes, ensuring maximum safety and reliability.3. Commitment to Sustainability (150 words)In an age where sustainability is paramount in industrial practices, {Company Name} has taken significant strides to minimize its environmental impact. As part of its commitment to sustainable development, the company has implemented energy-efficient manufacturing processes and optimized its supply chain to reduce carbon emissions.Furthermore, {Company Name} actively promotes the use of recycled steel, contributing to the reduction of natural resource consumption. By utilizing recycled materials, the company minimizes waste and supports a circular economy, aligning its business practices with global efforts to combat climate change.{Company Name} maintains a strong focus on the responsible disposal of waste and pollutants, ensuring compliance with environmental regulations. By adopting eco-friendly practices, the company not only minimizes its footprint but also sets an industry standard for sustainable manufacturing.4. Collaborative Partnerships for Continuous Improvement (150 words){Company Name} believes in fostering collaborative partnerships with clients, suppliers, and industry experts to drive continuous improvement. By working closely with customers, the company gains insights into their specific needs and preferences, allowing for the development of customized solutions.In addition, {Company Name} partners with suppliers who share their dedication to quality and innovation. This collaborative approach ensures a reliable supply chain, enabling the company to consistently deliver steel welded tubes of the highest standards.Furthermore, {Company Name} actively engages with industry experts, research institutions, and associations to stay abreast of the latest developments and trends. By participating in conferences and sharing knowledge, the company contributes to the growth and advancement of the steel welded tube industry as a whole.Conclusion:{Company Name} continues to lead the steel welded tube industry, pushing the boundaries of innovation and setting new benchmarks for quality and performance. Through its investment in cutting-edge technology, commitment to superior materials, sustainable practices, and collaborative partnerships, {Company Name} remains at the forefront of the industry, delivering exemplary products to customers worldwide.
Exciting Updates on the Latest Cast for Shaft 2 Unveiled
The highly anticipated upcoming action-comedy film Shaft 2 has announced its star-studded cast. Led by the iconic Samuel L. Jackson, who reprises his role as John Shaft II, the film boasts a talented ensemble of actors including Regina Hall, Method Man, Alexandra Shipp, and Avan Jogia.The Shaft franchise has a rich history, with the first film releasing back in 1971 and featuring Richard Roundtree in the titular role. The franchise returned in 2000 with Jackson playing the character of John Shaft's nephew, who takes up the family business of private investigation in modern-day New York City.Shaft 2 will see Jackson's character joining forces with his estranged son JJ, played by Jogia, to take down a drug lord who is terrorizing Harlem. Along the way, they team up with old and new allies, including Hall's character, a no-nonsense NYPD detective, and Method Man's character, a street-smart informant.The film has garnered a lot of attention for its diverse cast, which includes several actors of color in leading roles. Shipp, who gained popularity for her role in the X-Men franchise, plays JJ's love interest and a computer hacker who assists the duo in their mission."Representation matters, both in front of and behind the camera," said the film's producer, Marcus King. "We wanted to make sure that the cast reflects the city of New York, which is a melting pot of cultures and backgrounds."The film is being produced by New Line Cinema, a division of Warner Bros. Pictures. Shaft 2 is directed by Tim Story, who has previously worked with Jackson on the highly successful Fantastic Four films."We wanted to create a film that pays homage to the original Shaft films and yet feels fresh and relevant to today's audience," said Story. "There's a lot of action and humor in the film, but at its core, it's a story about family and redemption."The cast and crew recently wrapped up filming in New York City, and the film is currently in post-production. The official release date has not been announced yet, but it is expected to hit theaters in 2022.Fans of the franchise and newcomers alike are eagerly anticipating the release of Shaft 2, which promises to be a thrilling and entertaining addition to the series. With a talented cast, an experienced director, and a proven production team, Shaft 2 is sure to deliver all the action, humor, and heart that audiences have come to expect from the franchise.
Main Cast Announced for Upcoming Film Adaptation
Shaft Movie Cast AnnouncedIt’s time for a blast from the past for all the fans of the iconic Shaft character. Warner Bros. Pictures has officially announced the cast for their upcoming modern-day edition of Shaft. Directed by Tim Story, with production by John Davis and written by Alex Barnow and Kenya Barris, this movie marks another addition to the cherished Shaft franchise. The movie is set to release on June 14, 2019.The new Shaft film will star Samuel L. Jackson reprising his role as John Shaft II from the 2000 movie Shaft. However, this time he will be joined by his son, an FBI agent, John Shaft Jr., played by Jesse T. Usher. The platinum-selling rapper and actor, {Name}, will also be joining the iconic cast as Shaft’s nemesis.The movie is based on the story of a young MIT graduate, John Shaft Jr., who enlists the help of his estranged father, John Shaft II, to uncover the truth behind the death of his best friend. Through their investigation, father and son must navigate through the criminal underworld and outwit their enemies to get to the bottom of the mystery.With a star cast and a story that’s infused with a perfect blend of action and drama, Shaft is all set to become the ultimate crowd-pleaser. Fans of the franchise can’t wait to see how the tale of the coolest man in the history of private investigation unfolds, and how the addition of Junior, played by Usher, impacts the legacy of John Shaft.Warner Bros. Pictures is a leading entertainment company that has produced a number of successful and critically acclaimed movies over the years. With a long history of producing high-quality films, the company is known for its focus on innovation, exceptional storytelling, and creating a truly immersive movie-watching experience.John Davis, the producer of the movie, has been associated with some of the biggest action movies of all time, including Predator, The Man from U.N.C.L.E., and The Firm. Meanwhile, Tim Story, the director of the movie, has directed movies such as Fantastic Four, Ride Along, and Think Like a Man.Alex Barnow, the writer of the movie, has worked on hugely successful TV shows such as The Goldbergs, Son of Zorn, and Mr. Sunshine. Kenya Barris, the other writer of the movie, is known for creating the award-winning show Black-ish and has previously written for movies such as Barbershop: The Next Cut and Girls Trip.The slick and stylized action scenes in the trailer and the intriguing storyline of Shaft have already piqued the curiosity of fans. All eyes are now set on the release of Shaft, as it promises to be an explosive and nostalgic experience for movie lovers.Warner Bros. Pictures has set high standards for its movies and Shaft is no exception. As the countdown to June 14, 2019, begins, audiences are eagerly waiting to see how this action-packed movie is going to take the Shaft franchise to new heights.
Top Tips for Choosing the Ideal Rotating Shaft Seal
Title: Rotating Shaft Seal Redefines Efficiency and Reliability in Industrial ApplicationsIntroduction:In today's fast-paced industrial landscape, companies depend on innovative solutions to enhance efficiency and reliability across various sectors. Among the many remarkable contributions to this field, the Rotating Shaft Seal, developed by a leading manufacturing company, has emerged as a game-changer. Designed to meet the demanding needs of industrial applications, this advanced seal offers unparalleled performance while ensuring durability, sealing effectiveness, and reduced maintenance requirements.Company Background:Established over a decade ago, this pioneering manufacturing company prides itself on its commitment to excellence, relentless innovation, and customer satisfaction. Known for their cutting-edge technology and customer-centric approach, the company has manufactured and supplied high-quality industrial solutions to customers worldwide. Leveraging their extensive research and development capabilities, they have consistently strived to surpass industry standards, ensuring that their products deliver exceptional performance, durability, and efficiency in all applications.Rotating Shaft Seal Overview:Developed by the company's team of engineers and experts, the Rotating Shaft Seal offers a revolutionary approach to sealing technology. This state-of-the-art solution is designed to meet the most demanding requirements in numerous industries, including automotive, manufacturing, oil and gas, food and beverage, and many others.Unparalleled Performance:The Rotating Shaft Seal boasts impressive features that set it apart from traditional seals. Its unique design combines precision engineering, advanced materials, and innovative sealing principles to provide exceptional performance, even in the harshest operating conditions. With high resistance to corrosion, abrasion, and extreme temperatures, this seal remains unaffected by the most challenging working environments. This durability ensures uninterrupted operations, reduces downtime, and translates into increased productivity for businesses.Enhanced Sealing Effectiveness:The seal's advanced design allows it to maintain a strong and consistent seal, preventing leakage and ensuring maximum protection against contaminants. This feature is particularly crucial in industries dealing with hazardous or sensitive materials and environments. Additionally, the seal's superior sealing effectiveness significantly reduces the risk of equipment failure, thus boosting safety measures while prolonging the lifespan of the machinery.Reduced Maintenance Requirements:One of the primary advantages of the Rotating Shaft Seal is its ability to minimize maintenance costs and efforts. By utilizing cutting-edge materials and precision engineering, this seal is engineered to eliminate the need for frequent and expensive maintenance procedures such as re-greasing or replacement. This not only saves valuable time and resources but also optimizes overall operational costs, making it an economically viable solution for businesses of any scale.Applications Across Industries:The Rotating Shaft Seal has garnered appreciation across diverse industries due to its versatile nature and adaptability. In the automotive sector, this seal ensures smooth performance, minimizes friction, and improves fuel efficiency. Manufacturers benefit from reduced equipment downtime and enhanced productivity. In the oil and gas industry, the seal's durability and resistance to corrosive elements ensure reliable operations even in the most challenging environments. Additionally, the food and beverage industry relies on this seal to maintain hygiene, prevent contamination, and comply with stringent regulations.Conclusion:As industries continue to evolve and demand higher performance levels from their machinery, the Rotating Shaft Seal represents a groundbreaking solution that meets these challenges head-on. Combining cutting-edge technology, durability, superior sealing effectiveness, and reduced maintenance requirements, this seal is a testament to the company's commitment to providing innovative solutions for industrial applications. With its unparalleled performance, businesses can enhance productivity, optimize costs, and ensure reliable operations, cementing its position as an indispensable asset in the modern industrial landscape.Disclaimer: The brand name has been removed to comply with OpenAI's use case policy.
Aluminum Milling Machining Parts for Efficient Manufacturing
Aluminum Milling Machining Parts Revolutionize Manufacturing Industry: Meeting Demand for Precision and EfficiencyIn a time where precision and efficiency are crucial for successful manufacturing, the introduction of advanced aluminum milling machining parts has revolutionized the industry. These innovative components, which have been produced to the highest industry standards, offer manufacturers a reliable solution to meet their increasing demands and overcome various challenges.Aluminum, a widely used material in industries such as aerospace, automotive, and electronics, possesses unique properties that make it ideal for machining applications. Its lightweight nature, high strength-to-weight ratio, and excellent thermal and electrical conductivity have made it a preferred choice for manufacturers across the globe.However, machining aluminum parts can be a complex and demanding process due to its unique characteristics. Traditional machining methods often struggle with aluminum's tendency to generate heat and clog tools, leading to decreased efficiency and precision. To address these challenges, the renowned machining parts manufacturer {} has developed a range of cutting-edge aluminum milling components that have garnered significant attention within the manufacturing industry.With its extensive experience and expertise in precision machining, {} has successfully designed and produced aluminum milling parts that deliver exceptional performance. These innovative components utilize advanced materials and cutting-edge manufacturing techniques to ensure accuracy, efficiency, and reliability.One of the key features of {}'s aluminum milling parts is their exceptional heat dissipation capabilities. By employing state-of-the-art designs, these parts effectively overcome the heat generation challenges associated with machining aluminum. This unique attribute not only extends tool life but also enhances overall machining efficiency. Manufacturers can now perform longer machining operations without interruptions, resulting in increased productivity and reduced downtime.Moreover, {}'s aluminum milling parts are designed to prevent chip clogging. Aluminum is known for its tendency to produce long, stringy chips that may interfere with the machining process. {} has addressed this issue by incorporating specialized chip-breaking features into their parts. These innovations ensure the smooth flow of chips, maximizing machining precision and minimizing the risk of tool damage.To further enhance the performance of their milling parts, {} has also developed advanced coatings that provide superior wear resistance. These coatings not only prolong the life of the parts but also reduce friction during machining, resulting in smoother operations and improved surface finishes. By combining their expertise in material selection and coating technology, {} has introduced a range of products that meet even the most demanding requirements of modern manufacturing processes.The introduction of {}'s aluminum milling machining parts has created a significant impact on the manufacturing industry. Manufacturers across various sectors can now experience improved productivity, reduced downtime, and enhanced machining precision. By utilizing these innovative components, companies have seen notable improvements in their overall manufacturing efficiency, allowing them to meet demanding production schedules and achieve higher levels of customer satisfaction.With a strong commitment to quality, {} continues to push the boundaries of aluminum machining technology. They relentlessly invest in research and development to stay ahead of the competition and provide manufacturers with cutting-edge solutions to their machining needs. By removing the brand name, these aluminum milling parts have become synonymous with reliability, efficiency, and precision within the manufacturing industry.In conclusion, the introduction of advanced aluminum milling machining parts has brought about a revolution in the manufacturing industry. These innovative components, developed and produced by {}, offer manufacturers a reliable solution to meet their growing demands for precision and efficiency. With their exceptional heat dissipation capabilities, chip-breaking features, and advanced coatings, these milling parts have significantly improved productivity and machining precision, setting new standards for the industry.
Decorative Square Pipe Flange for Sewer and Industrial Scenes - Available in Antique Silver, Iron and Rust Finishes
CNC Milling Parts Suppliers and Manufacturers in China - Professional Services Available for Your Needs (Page 5)
Title: Achieving Precision and Durability with Stainless Steel CNC Milling PartsIntroduction:In today's rapidly evolving manufacturing industry, precision and durability are paramount. To achieve these qualities, many companies in various sectors are turning to CNC milling parts made from stainless steel. This versatile and robust material, combined with advanced CNC milling technologies, ensures the production of high-quality components that withstand demanding applications. In this blog post, we will explore the benefits and applications of stainless steel CNC milling parts, shedding light on why they have become a preferred choice for manufacturers worldwide.1. Unrivaled Strength and Durability:Stainless steel is renowned for its exceptional strength and durability. It can withstand harsh conditions, corrosion, and extreme temperatures, making it ideal for various industries, including aerospace, automotive, medical, and machinery. When fabricated into CNC milling parts, stainless steel components exhibit exceptional resistance to wear and tear, ensuring a long service life. Whether you require intricate parts or heavy-duty components, stainless steel CNC milling parts lend themselves perfectly to any application, contributing to the overall longevity of your products.2. Precision and Complex Geometries:CNC milling is a cutting-edge manufacturing process capable of creating highly intricate and complex designs. By employing advanced CNC milling techniques, stainless steel parts can be produced with unrivaled precision and attention to detail. This precision allows for tight tolerances, ensuring components fit seamlessly with other parts during assembly. Whether it's micro-milling or producing large-scale components, stainless steel CNC milling parts offer the accuracy required for demanding applications.3. Versatile and Customizable:Stainless steel CNC milling parts can be tailored to accommodate a wide range of industry needs. Manufacturers can choose from various stainless steel grades, each offering unique properties such as corrosion resistance, temperature resistance, or magnetic qualities. With the ability to modify composition, surface finishes, and hardness levels, stainless steel CNC milling parts are highly customizable to meet specific requirements. This versatility allows for adaptability across numerous industries, ensuring optimal performance and reliability in various applications.4. Cost-effectiveness and Time Efficiency:While stainless steel itself may have a higher initial cost compared to other materials, the long-term benefits outweigh the investment. Stainless steel CNC milling parts are exceptionally durable and require minimal maintenance and replacement, reducing overall costs in the long run. Additionally, CNC milling techniques offer speed and efficiency during the production process. Automated milling provides consistent results, eliminating human error and reducing manufacturing time. This cost-effectiveness and time efficiency result in enhanced productivity for manufacturers worldwide.Conclusion:Stainless steel CNC milling parts have revolutionized the manufacturing industry, providing unparalleled strength, precision, and durability. With the ability to withstand demanding applications, these components have become essential for a wide range of industries. Whether it's achieving intricate designs or producing heavy-duty components, stainless steel CNC milling parts consistently deliver exceptional performance. By investing in stainless steel CNC milling parts, manufacturers benefit from cost-effectiveness, time efficiency, and the confidence that their products will withstand the test of time. As the global manufacturing industry continues to evolve, stainless steel CNC milling parts are set to fulfill the ever-growing need for high-quality, reliable components.
Find Reliable Expansion Joints for Your Plant with Same or Next Day Delivery
Title: Understanding Flanged Rubber Expansion Joints: A Comprehensive GuideIntroduction:In industrial applications, ensuring the seamless operation and longevity of a plant is crucial. One often overlooked component that plays a critical role in this regard is the flanged rubber expansion joint. These flexible connectors are specifically designed to absorb movement, reduce vibration, and accommodate changes in pipe size, making them an indispensable part of any fluid handling system. In this blog, we will explore the fascinating world of flanged rubber expansion joints, their benefits, applications, and the factors to consider when choosing the right one for your project.Flanged Rubber Expansion Joints: Understanding the BasicsFlanged rubber expansion joints are precision-engineered connectors that provide the necessary flexibility to pipes and ductwork in various systems. They are comprised of reinforced rubber, fabric, or metal bellow sections, which allow for axial, lateral, and angular displacements. The primary function of these expansion joints is to compensate for thermal expansion, vibration, or movement caused by ground settlement or seismic activity. They also help in reducing noise transmission and absorbing shock to protect equipment and infrastructure.Benefits of Flanged Rubber Expansion Joints1. Flexibility and Movement Absorption: Flanged rubber expansion joints are designed to accommodate movement, angular deflection, and vibration. They act as a flexible link between pipe sections, absorbing both axial and lateral movements caused by thermal expansion or contraction, thereby preventing stress and damage to the system.2. Noise and Vibration Reduction: The rubber construction of these expansion joints helps in reducing noise transmission in the system, making them ideal for installations where noise control is critical. Additionally, they effectively dampen vibrations, preventing them from spreading throughout the system and causing potential damage.3. Corrosion Resistance: Flanged rubber expansion joints are resistant to a wide range of corrosive fluids, making them suitable for various industrial applications where the conveyed media may have corrosive properties. This property adds to their longevity and reduces maintenance costs.4. Fast Installation and Cost-Effectiveness: With various flange options available, these expansion joints can be easily fitted into existing or new piping systems. Their availability in stock and prompt delivery further ensures minimal downtime during installation or replacement.Applications of Flanged Rubber Expansion Joints1. HVAC Systems: Flanged rubber expansion joints are commonly used in heating, ventilation, and air conditioning (HVAC) systems to accommodate thermal expansion and vibration, ensuring the smooth operation of the system.2. Power Generation: Thermal power plants, nuclear power plants, and other energy generation facilities utilize flanged rubber expansion joints to absorb thermal expansion and protect critical components, such as pumps, turbines, and boilers.3. Chemical Processing: Flanged rubber expansion joints find extensive use in chemical processing plants, where they accommodate the corrosive nature of chemicals, compensate for thermal movement, and reduce vibration, ensuring safety and prolonged equipment life.4. Water and Wastewater Treatment: Municipal water treatment plants, sewage treatment facilities, and desalination plants all employ flanged rubber expansion joints to handle the constant movement of pipes due to temperature fluctuations and pressure changes, as well as to reduce noise and vibration.Choosing the Right Flanged Rubber Expansion JointWhen selecting a flanged rubber expansion joint for your specific application, several factors need to be considered:1. Operating Conditions: Ensure that the expansion joint is suitable for the temperature, pressure, and media conveyed in your system. This includes assessing the corrosiveness, abrasiveness, and the presence of any particulates in the fluid.2. Movement Capability: Determine the extent and type of movement (axial, lateral, angular) that may occur in the system, ensuring the expansion joint's design is capable of accommodating it.3. Flange Compatibility: Check that the flange design of the expansion joint matches that of the existing or adjoining pipes, ensuring a secure and leak-free connection.4. Size and Construction: Consider the size requirements, as well as the construction material of the expansion joint, to ensure it can withstand the demands of your specific application.Conclusion:Flanged rubber expansion joints are indispensable components of fluid handling systems, providing flexibility and accommodating the movements caused by thermal expansion, vibration, and ground settlement. Their ability to reduce noise, absorb shock, and resist corrosion makes them vital in ensuring the smooth operation and longevity of industrial plants. By considering the crucial factors discussed above, you can confidently choose the right flanged rubber expansion joint for your application, minimizing downtime, and optimizing safety.Remember, when it comes to the reliable and efficient operation of your plant, the appropriate choice of flanged rubber expansion joints is key.
Ultimate Guide: Exploring the Features and Uses of Stainless Steel Blind Flanges
Title: Stainless Steel Blind Flange: A High-Quality Solution for Seamless Construction ProjectsIntroduction:[Company Name], a leading manufacturer and supplier of high-performance industrial products, is pleased to present its exceptional range of stainless steel blind flanges. These flanges offer unparalleled strength, reliability, and versatility, making them an ideal choice for seamless construction projects across various industries.Body:1. Overview of Stainless Steel Blind Flange:Stainless steel blind flanges are vital components in pipeline systems, acting as a permanent or temporary seal for piping openings. They are designed to cover the ends of pipelines, preventing the flow of fluids or gases and ensuring safety and integrity. The blind flanges from [Company Name] are manufactured using the highest quality stainless steel, which provides exceptional resistance to corrosion, high temperatures, and pressure. These features make them ideal for demanding applications in industries such as oil and gas, chemical, petrochemical, and power generation.2. Unmatched Strength and Reliability:[Company Name]'s stainless steel blind flanges are engineered to deliver unparalleled strength and reliability, reinforcing the overall performance of pipeline systems. The flanges are forged from premium-grade stainless steel, ensuring exceptional durability and resistance to wear and tear. With their robust construction, they are capable of withstanding extreme conditions, including high pressures and temperatures, while maintaining their structural integrity for extended periods.3. Corrosion Resistance:One of the significant advantages of stainless steel blind flanges is their remarkable resistance to corrosion. The stainless steel used in their manufacturing contains a high percentage of chromium, which forms a protective layer on the surface, preventing oxidation and corrosion. This feature is particularly crucial for industries dealing with corrosive substances, as it ensures the longevity and reliability of the pipeline systems, minimizing the need for frequent maintenance or replacement.4. Versatility for Various Applications:Stainless steel blind flanges are designed to meet the diverse needs of different industries and applications. With their compatibility to various piping systems, these flanges offer flexibility in installation, facilitating easy and efficient pipeline assembly and disassembly. Furthermore, they can be customized to meet specific requirements, including size, pressure ratings, and surface finishes, ensuring a perfect fit for any project.5. Compliance with International Standards:[Company Name] is committed to delivering products of the highest quality and adheres to rigorous industry standards. The stainless steel blind flanges are meticulously manufactured in accordance with international specifications and standards, such as ASME, ANSI, DIN, and EN. This ensures that customers receive products that meet or exceed their expectations, guaranteeing safety, reliability, and compliance.6. Commitment to Customer Satisfaction:At [Company Name], customer satisfaction is our top priority. We strive to provide exceptional customer service, technical support, and timely delivery to meet the unique needs and demands of our valued clients. Our team of experts is available to offer guidance and assistance throughout the project, ensuring successful implementation and seamless integration of our stainless steel blind flanges.Conclusion:With their exceptional strength, reliability, corrosion resistance, and versatility, stainless steel blind flanges from [Company Name] are the ideal solution for seamless construction projects across various industries. These flanges not only offer top-notch performance and durability but also comply with international standards, providing customers with peace of mind and confidence. Choose [Company Name] for your blind flange requirements and experience the excellence we deliver in every product.